Effective maintenance management relies on accurate, high-quality maintenance data. Yet, human error often leads to inaccurate information being entered into computerized maintenance management system (CMMS) software, compromising its reliability and usefulness. To combat this, many organizations implement barcode systems that streamline data entry, lookup, and retrieval. This article explores how barcode systems work and how they enhance maintenance operations by improving data accuracy, productivity, and day-to-day efficiency.
What is a Barcode System?
A barcode system is a combination of hardware and software used to automate data collection through the use of barcodes. This includes:
- Barcode software which generates and manages barcode data
- Barcodes which encode alphanumeric data
- Barcode labels on which barcodes are printed and attached to assets
- Barcode printers used to print physical barcode labels
- Barcode scanners which read barcodes
- Other software which interprets the data
Barcoding systems are used across industries – from retail and logistics to libraries and event management – to streamline data capture and tracking. In maintenance environments, they are useful for MRO inventory management and asset tagging. Many CMMS solutions include built-in barcode functionality to help enter data, track inventory, and maintain accurate records.
How Barcode Systems Work
Barcode systems encode data into a visual pattern (the barcode), that can be quickly scanned and interpreted by a computer system. Here’s how the different components of the system work together:
- Barcode Generation: Maintenance teams use barcode software to create unique codes for their assets, spare parts, tools, or other items.
- Printing Labels: These barcodes are printed onto durable barcode labels using a barcode printer.
- Applying Labels: Labels are attached to equipment, parts, or stocking locations.
- Barcode Scanning: Technicians use barcode scanners – or mobile devices – to scan assets and inventory while carrying out maintenance tasks.
- Integration with CMMS: Scanned data is used to populate fields, navigate to records, or automatically update information within the CMMS.
Using a barcode system eliminates the need for manual data entry, reduces human error, and improves the accuracy and speed of data entry and retrieval. Ultimately, this results in faster response times, greater productivity, and more reliable maintenance records.
Understanding Barcode Technology
To get the most value out of a barcode system, it’s important to understand how each component contributes to the overall process. From the type of barcode used to the software that uses encoded data, every piece plays a role in efficient maintenance operations. The following sections explore each component of a barcode system and how they work together.
Barcodes
A barcode is a representation of data in a coded format, usually in the form of parallel lines or a square of strategically spaced pixels. In simple terms, a barcode is a visual “language” that can be read by scanners and software. Barcodes, generated through barcode software, are printed onto labels using specialized printers.
Barcodes represent information that uniquely identifies an asset or inventory item, such as a name or number. The combinations of black and white spaces in a barcode represent alphanumeric characters and follow preset rules depending on their type. When scanned with a laser light from a barcode scanner, the encoded information is translated into readable data.
Types of Barcodes
Understanding the different types of barcodes helps maintenance teams select the best format for labeling assets based on amount of data, available scanning technology, and durability needs. Barcodes fall into two main categories: 1-dimensional (1D) or 2-dimensional (2D).
- 1D barcodes are comprised of vertical lines and numbers on a single horizontal line, and are used to encode a small string of alphanumeric characters.
- 2D barcodes are composed using 2-dimensional symbols and shapes. Due to their increased size and dimension, 2D barcodes are used to encode larger amounts of data.
1-dimensional Barcodes

Examples of 1-dimensional barcodes (left to right): Code 128, UPC, and Code 39
- Code 39: One of the oldest barcode types; can encode numbers and upper case letter. The encoded value can be any length that fits on the label.
- Code 128: Encodes the full American Standard Code for Information Exchange (ASCII) 128 character set; compact and automatically optimizes length by switching between character sets.
- Interleaved 2 of 5: Numeric-only barcode used to encode pairs of digits; therefore, the number of digits must be even.
- Universal Product Code (UPC): Commonly found on retail products; originally developed for grocery stores to speed up checkout and inventory tracking.
- European Article Number (EAN): The international equivalent to the UPC, used primarily outside of the United States and Canada.
2-dimensional Barcodes
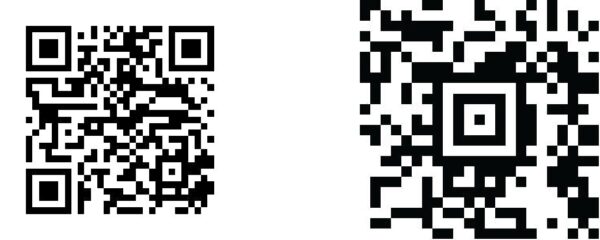
Examples of 2-dimensional barcodes: QR code (left) and Aztec Code (right).
- Quick Response (QR) Code: Newest type of barcode; is used to link to web pages, add contacts, scan event tickets, and much more.
- Aztec Code: Designed to be more compact than a QR code, featuring a bull’s-eye resembling an Aztec pyramid.
- PDF417: A 2D stacked linear barcode used for driver licenses and other government materials; can be linked to more than one file.
- Data Matrix: A 2D square that can encode huge amounts of information in one space; used in electronics and healthcare
Barcode Scanners
A barcode scanner is an input device used to scan or read a barcode with a laser or camera. Like a keyboard, barcode scanners connect to a computer and enter encoded barcode data into a software application such as an inventory management system or CMMS. Barcode scanners can be either wired or wireless. CMMS mobile apps also use a device’s camera to scan barcodes.
Wired Barcode Scanners
Wired barcode scanners are handheld scanners connected to a computer via physical cord, similar to your computer’s mouse, keyboard, monitors, and other plug-in devices. They are commonly used in retail settings to scan barcode labels on larger items that do not fit on the checkout lane belt.
Wired scanners work well in small stockrooms where the cord can reach where needed, or for barcode scanning small items that are easily moved to the scanner area. Because wired scanners tether an employee to a workstation, they are generally considered less convenient than wireless scanners; however, they often cost less.
Wireless Barcode Scanners
Wireless barcode scanners are the most common types of barcode scanners found in a maintenance environment. They, too, are handheld, but are not attached by a cord. Instead, wireless scanners use radio waves to transmit data via a paired USB receiver or Bluetooth connection.
Wireless scanners are preferred over wired barcode scanners because of the mobility afforded to employees. They are easy to carry and can be used to scan assets or inventory in a wider area, though there are some limitations to their range.
Mobile Computer Scanners
Wireless scanners are also integrated into mobile computers that combine the processing power of an onboard computer with the scanning functionality of wireless scanners. While wired and wireless barcode scanners must be connected to desktop computer (or laptop) in order to function, mobile computer scanners allow users to move freely and perform tasks anywhere. However, special software, docking hardware, and drivers are required for use.
Mobile Devices with Barcode Scanning Support
Most modern smart devices have built-in camera functionality that can read barcodes, use a barcode scanning app, or support barcode scanner attachments. This allows maintenance technicians using mobile CMMS software to get the full benefit of barcode scanning while maintaining access to mobile work orders and other maintenance data.
Barcode Printers and Labels
Barcode printers are specialized printers used for printing barcode labels for industrial purposes. There is a wide variety of printer options available, offering different degrees of print volume, mobility, type of printing, and printing technology. In addition, organizations must consider the type and size of barcodes to use, as well as the material used for barcode labels, ensuring they hold up against hot, cold, dusty, or wet environments.
Barcode Software
Barcode software is a specialized computer program used to generate the 1D or 2D barcodes that get printed onto labels and read by scanners. While there are many standalone barcode software options available on the market, many do not offer the MRO inventory management capabilities required for maintenance management.
Fortunately, many CMMS solutions include barcoding functionality, so no dedicated barcode software is required. Organizations that desire to implement a barcode system are responsible for selecting compatible scanners, printers, and labels.
Applications of Barcodes in Maintenance Management
Barcode technology enhances many day-to-day maintenance management activities. The sections below describe common applications of barcodes in maintenance environments.
Asset Tagging and Tracking
Asset tags are barcode labels that uniquely identify physical assets and are directly applied to asset exteriors for tracking purposes. In an ideal scenario, asset tags allow maintenance staff to walk up to an asset, scan the barcode, and perform some action using their CMMS. For example, the system might allow users to look up asset details, view maintenance records, or create a work order for the asset.
Asset tags are useful for organizations that have a large number of assets to maintain. Scanning barcodes reduces human error, ensuring technicians access and record accurate maintenance data for the specified asset.
Because asset tags are affixed to the asset, barcode labels must be able to withstand extreme temperatures, moisture, debris, and vibration without being compromised or lost. Incomplete or missing information invalidates the value of the barcodes. Organizations must choose the barcode printer and labeling materials that best suits their needs.
Read more: What is Asset Management in Maintenance Operations?
Tool Tracking
Durable assets like tools are also commonly tracked via barcodes. This is because, unlike equipment assets which are largely stationary (except for vehicles), tools are mobile, shared among staff, and change location often. Barcoded tools allow the maintenance department to monitor exactly which tools are checked out, their current locations, and how many are available in inventory for use.
Tool movement is tracked through a check-in/check-out process using barcodes, similar to borrowing books from a library. When a tool is needed, technicians scan the barcode to check it out, reserving it for use. When the tool is returned, it is scanned back in to its storage location.
Read more: What is MRO Inventory Control?
MRO Inventory Management
Organizations typically stock hundreds, thousands, and even tens of thousands (or more) of MRO items within a stockroom. The sheer volume of unique inventory items makes it necessary to avoid misidentifying inventory items when completing work orders or replenishing the stockroom.
When applied to stockroom racks, shelves, and bins, barcode labels are useful for identifying the items stored there. This is useful for verifying parts pulled for maintenance work, adjusting part quantities when making kits, and performing physical inventory counts. Stockroom employees save time by scanning barcodes instead of manually typing numbers into the CMMS.
Alternatively, barcodes might exist in a master binder that lists all inventory items along with their corresponding barcodes. When the location of an inventory item is unknown, employees can look up its location in the CMMS by scanning the barcode information into a search field. The system then identifies the exact aisle, rack, shelf, and bin location of the item.
Read more: What is MRO Inventory Management?
Purchasing and Receiving
Barcodes are a useful tool when used with a CMMS’s purchasing and receiving functionality. When new inventory items arrive and need to be received, employees look up purchase orders by scanning a barcode on the physical PO form. From there, employees then update the status and quantities of incoming purchase order items. Having barcodes in place makes this process much faster and easier, especially when several items are received at once.
Organizations that track vendor item numbers are able to scan the barcode labels on incoming items and match them up with inventory records in the CMMS. Then, organizations are able to generate barcode labels that follow the organization’s internal numbering scheme for tracking and stocking purposes.
Barcoded Documents
CMMS software with barcode capability can generate barcoded paper documents, such as purchase orders and work orders. When these records need to be looked up and updated in the CMMS, all users need to do is click into a search field and scan the barcode. This is a huge timesaver when many items are received at once, or when a batch of work orders is ready to be closed.
CMMS Ease of Use
Depending on the CMMS, barcodes can provide shortcuts to valuable information. For example, clicking through multiple screens takes much longer than scanning a barcode. After the system recognizes the asset (or document), it can take the user to the record details or present the user with a list of options for what to do next.
Even if scanning a barcode only reduces user interaction by one click, those clicks add up over time. After all, the less time a technician spends clicking around in the CMMS, the more time he can spend actually performing maintenance work.
Read More: What Makes CMMS Software Easy to Use?
Benefits of Barcoding Technology in Maintenance Management
The applications of barcodes span nearly every major facet of maintenance management. Fortunately, many CMMS software solutions include barcode technology, thereby making it easier to incorporate barcoding into your maintenance process. As this article demonstrates, there are many advantages to barcoding:
- Reduced Human Error: Barcode scanning allows information to be entered into a CMMS using a scanned code instead of manual entry, thereby preventing mistakes and improving the accuracy of maintenance data.
- Increased Productivity: Once fully implemented, a barcode system allows maintenance workers to quickly locate information or take additional action using the CMMS. Wireless scanners and mobile barcode scanning allow employees to stay productive.
- Better Decision-Making: When using accurate data, maintenance organizations are able to make smarter decisions about asset maintenance, inventory purchasing, maintenance schedules, and more. This leads to more efficient operations and lower maintenance costs.
- Improved Return on Investment (ROI): Over time, organizations will be able to grow into using more advanced features of their CMMS. Combining powerful CMMS software with a barcode system provides additional long-term value to the organization, increasing the CMMS ROI.
- Increased User Adoption: Employees are more likely to adopt a system that is easy to use. Barcode scanning provides an easy data entry method for employees of all computer skill levels.
Improve Accuracy and Productivity with FTMaintenance Select
Many organizations struggle with tracking assets and inventory, and experience unexpected shrinkage, stockouts, and delays. FTMaintenance Select’s barcode services save you time in identifying your assets and introduce a high level of accuracy into your organization’s everyday data entry. Contact us today to learn more about the FTMaintenance Select barcode system.