An inevitable result of the manufacturing process is the creation of waste, and it comes in many forms. Implementing lean manufacturing techniques enables organizations to target and eliminate waste, leading to more productivity and ultimately, higher profits.
Because the maintenance team is responsible for equipment maintenance, it must also eliminate waste in maintenance processes that threaten efficient production. This article provides an introduction to lean management and discusses how the maintenance team contributes to a lean manufacturing system.
What is Lean Manufacturing?
According to the American Society for Quality (ASQ), “lean manufacturing is a system of techniques and activities for running a manufacturing or service operation” with the goal of maximizing the value delivered to customers. This is done by eliminating waste (i.e., non-value-adding activities) at each stage of the production process.
Origins of Lean Manufacturing
Lean manufacturing originates in the automotive industry, starting with the founder of Ford Motor Company, Henry Ford. Ford’s moving assembly line process cut out much inefficiency from manual processing to make mass production possible. Over time, the Toyota Motor Corporation continued to improve upon Ford’s idea to create the Toyota Production System, which focuses on “the complete elimination of all waste in pursuit of the most efficient methods.”
Today, lean manufacturing concepts are used in many industries including:
- Automotive manufacturing
- Footwear and apparel manufacturing
- Textile manufacturing
- Healthcare
- Food and beverage
- Construction
- Government
- Hospitality
Principles of Lean Manufacturing
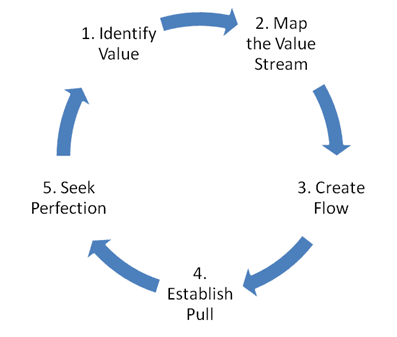
Image derived from Lean Enterprise Institute at https://www.lean.org/lexicon-terms/lean-thinking-and-practice/
There are 5 main lean manufacturing principles that guide organizations on how to optimize their production process:
- Identify value: Understand the value customers place on your products (i.e., what problems they need to solve).
- Map the value stream: Visualize every step of your manufacturing process, from raw materials to delivery, to identify which activities add value versus create waste.
- Create flow: Optimize your manufacturing process by eliminating bottlenecks, reducing changeover time, and leveling production.
- Establish pull: Manufacture product only when there is demand.
- Seek perfection: Strive towards excellence by making ongoing, incremental changes towards your goal.
8 Wastes of Lean Manufacturing
If waste is to be eliminated, one must know what types of waste exist. As mentioned earlier, waste is any activity that does not add value to the customer. Lean manufacturing identifies several types of waste within the manufacturing process.
- Transportation: Unnecessary transportation of employees, tools, inventory, or equipment
- Inventory: Producing quantities of inventory that exceed demand
- Motion: Unnecessary movement of people or equipment
- Waiting: Idle time, such as waiting for materials to arrive or for equipment maintenance to be complete
- Overproduction: Manufacturing product before it is truly needed
- Over-processing: Adding features to a product that are not required by the customer
- Defects: Producing products that are not fit for use, resulting in rework or scrap
- Unused talent: Not taking worker’s ideas and input into account when making decisions
The Toyota Production System further organizes waste into the following three categories:
- Muda (wastefulness): Waste that is produce by unnecessary, non-value-adding activities, materials, and other work.
- Mura (unevenness): Waste due to fluctuations in demand, resulting in an uneven work pace.
- Muri (overburden): Waste caused by overworking people or machines; working in an unsustainable way.
Lean Manufacturing and Maintenance Management
Lean manufacturing focuses on production – so what does it mean for maintenance organizations? Since maintenance and production are so closely related, one could justify that adequate maintenance enables lean manufacturing. Therefore, any changes to the production process also require changes to the maintenance process.
For example, problems encountered in a continuous flow process shut down the entire production line, requiring maintenance to either respond quicker to downtime or implement proactive maintenance techniques that prevent such problems from occurring. Each of these solutions requires changes to maintenance operations, techniques, tools, and management.
Keep in mind that the lean philosophy applies to any process or function, including maintenance. “Lean maintenance” aims to optimize maintenance and asset management activities, which is commonly plagued with waste caused by excessive MRO inventory, over- or under-maintaining equipment, and inefficient maintenance tracking.
Implementing lean maintenance can improve productivity, reduce maintenance costs, increase asset reliability and longevity, and make the maintenance team look more competent. Additionally, lean maintenance gives you the ability to do more maintenance work with the same or fewer resources. Given the maintenance technician shortage, finding ways to reduce maintenance costs without losing employees is especially important.
Lean Tools and Techniques Used by Maintenance Organizations
Given its scope, lean manufacturing utilizes multiple tools and techniques to eliminate waste and improve efficiency. We have highlighted the lean tools most relevant to maintenance management in this article. A more comprehensive list is provided on LeanProduction.com.
Lean Tools
The following tools are part of the lean methodology in general, though we discuss how they can be applied to maintenance management.
5S
5S is an organization system that aims to create efficient, effective, and safe work environments. Also part of the Toyota Production System, 5S seeks to reduce waste in employee workspaces. 5S gets its name from the 5 steps it includes:
- Sort (seiri): Remove any unnecessary or unwanted items from the workspace.
- Set in Order (seiton): Arrange items in a logical, organized manner.
- Shine (seiso): Clean the workspace.
- Standardize (seiketsu): Make sorting, setting in order, and shining routine activities.
- Sustain (shitsuke): Form long-lasting habits and update as necessary.
One of the most common workspaces to improve through 5S is the maintenance storeroom. Storerooms in many organizations are messy, cluttered, and create several inefficiencies that lead to higher MRO inventory costs. However, an organized storeroom can improve efficiency by 10% to 30%. More on this topic can be found in our article, How to Organize Your Maintenance Storeroom.
Just-In-Time Inventory Management
Just-in-Time (JIT) inventory management is an inventory management technique that enables organizations to meet demand while working with minimal inventory. For production, this means only producing enough goods to satisfy customer orders. Materials are ordered to arrive “just in time” to fulfill the order.
In a maintenance context, demand is typically driven by preventive maintenance (PM) because tasks are scheduled and the required part quantities are known. Organizations may also refer to maintenance reports that show historical part usage trends to estimate demand for corrective maintenance (CM).
Using JIT inventory management for MRO items, organizations may opt not to stock particular items that can be sourced locally and obtained quickly when needed. Doing so saves storeroom space and inventory management effort. Just-in-Time inventory management is discussed further in our article, MRO Inventory Optimization Techniques.
Poka-yoke (Mistake-proofing)
Poka-yoke, or mistake-proofing, means to minimize the number of mistakes employees make in order to avoid defects, rework, or scrap. Maintenance managers can limit employee errors by:
- Improving the accuracy of data entry through barcode scanning
- Providing step-by-step instructions for routine maintenance tasks
- Developing and communicating clear policies and procedures
- Clearly labeling equipment, storerooms, stocking locations, and tools for easy identification
- Providing ongoing training opportunities
- Holding employees accountable for performing quality maintenance work
- Implementing a work order approvals process to ensure work is done correctly
- Providing quick access to a digital library of maintenance documentation
Putting measures in place to prevent common errors leads to vast improvements in the quality and consistency of maintenance work. This translates to improved asset reliability, extended asset life, and lower maintenance costs.
Kaizen (Continuous Improvement)
One of, if not the most important, element of lean is kaizen, meaning “change for the better”. The idea behind kaizen is to examine inefficient processes or recurring tasks and make small, incremental improvements over time. An important aspect of kaizen is to document your process and measure it over time to see if changes achieve the intended result.
Lean Maintenance Tools and Techniques
There are several tools and techniques maintenance teams utilize to support a lean manufacturing approach.
Computerized Maintenance Management System (CMMS) Software
Many maintenance organizations still rely on manual maintenance tracking systems to manage their maintenance operations. These outdated systems are simply too cumbersome and ineffective for managing today’s complex maintenance needs.
A computerized maintenance management system (CMMS) is a centralized platform for documenting, managing, and tracking maintenance activities. It provides you with real-time access to important maintenance information, allowing you to increase your productivity and efficiency. Automated features reduce the burden of managing day-to-day administrative tasks related to work order management, maintenance planning and scheduling, asset management, and other aspects of your maintenance operation.
Total Productive Maintenance (TPM)
Total productive maintenance (TPM) is a system of maximizing asset availability by taking an organization-wide approach to maintenance. One of the main pillars of TPM is autonomous maintenance, which places the responsibility of performing simple preventive maintenance tasks on machine operators. Doing so increases the operator’s knowledge of their equipment, allowing them to spot and address small issues before they become big problems that cause downtime.
Failure Analysis
Unexpected asset failures result in lost production time. While many organizations simply treat the symptoms of failure in order to return machines to operation, others perform failure analysis to determine how to avoid future failures. There are many methods of failure analysis including:
- Failure, Cause, and Remedy Codes: the process of using a CMMS to codify and standardize documentation of the type of failure, its cause, and its solution.
- Root Cause Analysis (RCA): the process of identifying the origins of an asset failure and developing an approach to resolve it.
- Five Whys: a method of executing root cause analysis by asking “why” five times.
- Failure Modes and Effects Analysis (FMEA): a systematic way of determining all possible ways assets can fail, their potential causes, and risk to the organization.
Though each of these methods varies in complexity, all aim to prevent or mitigate the effects of failure, thereby minimizing interruptions to production.
Reliability-Centered Maintenance (RCM)
Reliability-centered maintenance (RCM) is a corporate-level, proactive maintenance strategy that determines the most cost-effective maintenance techniques to maximize asset reliability. It considers the inherent design of equipment, taking into account: equipment function and performance standards, functional failures, failure modes, and failure effects. Based on this analysis, organizations then determine the appropriate tasks to eliminate, detect, reduce the frequency of occurrence of, or reduce the impact of each failure.
As its name suggests, RCM is focused on reliability, or reducing the frequency of asset failure. Reliable assets perform their intended function for longer periods of time without failure (so long as they are used under their stated operating conditions). RCM reduces lost production time caused by unexpected failures and waiting for maintenance to make repairs.
Predictive Maintenance (PdM)
Predictive maintenance (PdM) is a maintenance technique that forecasts when assets will fail by analyzing real-time and historical asset performance data. Compared to preventive maintenance, which is performed according to set intervals, predictive maintenance allows maintenance to be scheduled and performed only when it is truly needed. As a result, the maintenance team can sharply reduce unscheduled downtime and the severity of failures, when they do occur. This leads to optimal availability, reliability, and production capacity.
Key Performance Indicators (KPIs)
Tracking key performance indicators (KPIs) helps you determine whether changes to your maintenance process are having the desired impact. The metrics you track depend largely on what’s important to your organization, the process you are trying to optimize, and the type of waste you seek to eliminate. Common lean maintenance KPIs include:
- Mean Time to Repair (MTTR)
- Mean Time Between Failure (MTBF)
- Overall Equipment Effectiveness (OEE)
Explore our collection of maintenance KPI articles: |
Maximize the Efficiency of Your Maintenance Process with FTMaintenance Select
The main goal of lean manufacturing is to eliminate waste from the production process, which relies on the competence of the maintenance team. Using a CMMS like FTMaintenance Select is one of the best ways to create an efficient, mobilized, and connected maintenance team that supports lean initiatives. By automating essential tasks related to work order management, asset management, inventory management, and more, FTMaintenance Select empowers you to eliminate waste and make maintenance management easy. Request a demo today to learn more.