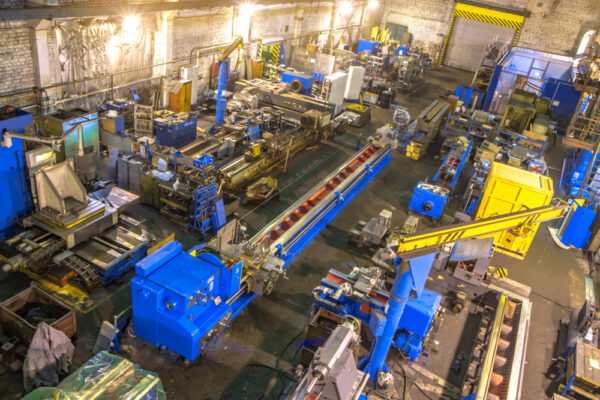
Compared to other aspects of asset management, organizations often overlook the importance of implementing effective asset naming conventions. Though often viewed as an administrative task, developing a reliable naming system helps standardize asset identification and makes it easier for anyone managing, tracking, or servicing equipment to understand and communicate about your assets.
In this complete guide, you’ll learn how to create a practical asset naming convention that brings clarity and efficiency to your maintenance operations.
What is an Asset Naming Convention?
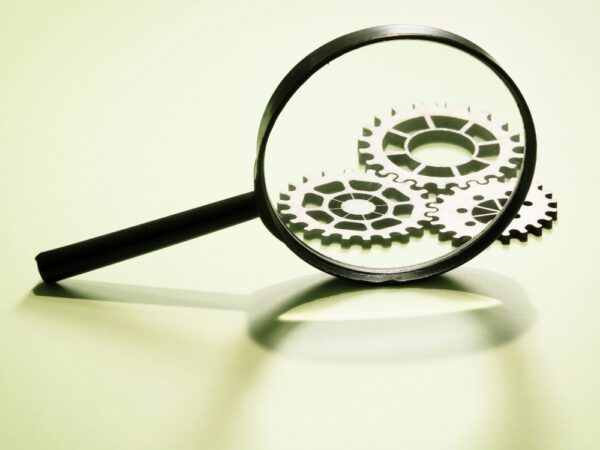
An asset naming convention is an agreed-upon set of rules for choosing the names and numbers used to identify your assets. As mentioned in our article, What is Asset Management?, identification plays an important role in asset management, helping maintenance teams know exactly what they are responsible for managing. Asset naming conventions are developed to ensure consistent identification and improve communication about specific equipment and machines.
In relation to implementing a computerized maintenance management system (CMMS), asset names are used to uniquely identify asset records within the system, making it easy for users to identify, select, and properly track maintenance against assets.
Clarifying Asset Names vs. Numbers
In a CMMS, every record typically includes both a unique identification number – either system-generated or user-provided – and a descriptive name. Though the term asset naming convention is commonly used to describe both of these components together, they serve different purposes:
- The asset name is a human-friendly label used by CMMS users to easily recognize the asset.
- The asset number, or ID, is a unique identifier used by the system to track and manage asset records. It is often codified to provide users with at-a-glance information about the record.
Why Asset Naming Conventions Matter
Can you imagine identifying tens to thousands of assets based solely on a description? Not only would it be exhausting and confusing, it would be highly inefficient. Naming assets makes them easy to identify – but simply assigning names isn’t enough.
The value of following a consistent asset naming convention is that anyone who interacts with your assets – whether now or in the future – can quickly understand what the names represent. By establishing a common “language” about your assets, you can ensure immediate recognition, improve communication across teams, and ensure efficient asset tracking in your CMMS.
You may not realize it, but you are likely already familiar with the concept of naming conventions. Let’s look at a few examples:
Example 1: Corporate Email Addresses
A common way organizations assign employee email addresses is to use a combination of their first and last name. For example, John Doe’s email address may be jdoe@mycompany.com or john.doe@mycompany.com, while James Smith’s would start jsmith or james.smith. This naming scheme is consistent and scalable – Derek Johnson becomes djohnson, Alice Matthews becomes amatthews, and so on.
Because of this pattern, it’s easy to guess Mark Jacob’s email address without need to ask, and there’s no confusion about who was assigned to the address. Of course, there may be exceptions to these rules to accommodate two people who share the same surname or initials, such as James Smith and John Smith. For example, James Smith’s address might be jsmith, while John Smith’s address may incorporate a middle initial (jdsmith) or number (jsmith2).
Example 2: Computer File Naming Conventions
Many organizations use file naming conventions to keep documents organized and easy to find. The University of Wisconsin-Madison’s Research Data Services provides students with clear recommendations for naming files and folders. Their example convention incorporates the following elements for a research file:
- The name of the lake and buoy from which data is collected
- A date code using the YYYY-MM-DD date format recommended by ISO 8601
- The version of the document
Using this system, a file named Mendota_Buoy6_20110711_v2 tells the user that data was collected from Lake Mendota, buoy number 6, on July 11, 2011, and that this is the second revision of the document.
Similarly, Purdue University’s Data Management for Undergraduate Researchers guide suggests that naming conventions include the following elements:
- A preview of the file’s content
- A logical way to organize files, such as a date in year-month-day format
- The responsible party
- A way to convey the work history
Using this system, the file named 20130503_DOEProject_DesignDocument_Smith_v2-01 is interpreted as version 2.01 of the design document for the DOE Project, created or updated by someone with the last name of “Smith” on May 3, 2013.
Example 3: Phone Numbers
In the United States, phone numbers follow a 10-digit format defined by the North American Numbering Plan (NANP), developed by AT&T. The format is typically represented as NXX-NXX-XXXX, where N represents any digit 2 – 9, and X represents any digit 0 – 9. The structure breaks down as follows:
- NXX: The Numbering Plan Area (NPA) code, commonly called an area code, which identifies a broad geographic region.
- NXX: The central office code or prefix, which identifies a more specific location or exchange within the area code.
- XXXX: The line number that designates the individual phone line or device.
Phone numbers don’t tell you everything about the person or business you are calling, but once you understand the structure, they provide helpful context before you even dial.
Importance of Asset Naming Conventions in Maintenance Management
The examples above demonstrate how a well-structured naming scheme makes it easier to interpret what something is. When applied to maintenance management, naming conventions are used to develop asset identifiers that workers can easily understand – appearing on asset tags, equipment labels, and in maintenance software.
In a CMMS, consistent naming helps users search, filter, and locate records more efficiently. Asset names often include meaningful details such as type, location, or unit number. Those same elements can be codified into asset numbers, making unique identifiers more useful and intuitive. This level of clarity ensures that all maintenance stakeholders – from technicians to operations managers – can consistently identify your assets, thereby improving the accuracy of maintenance tracking. It also simplifies the naming of new records in the system.
Beyond assets, naming conventions can also be applied to other maintenance-related resources. In a CMMS, every record needs to be uniquely identified – from inventory and vendors to tasks and labor resources. By formalizing your naming system, your organization can more easily create, find, and manage organized maintenance records.
Creating an Asset Naming Convention
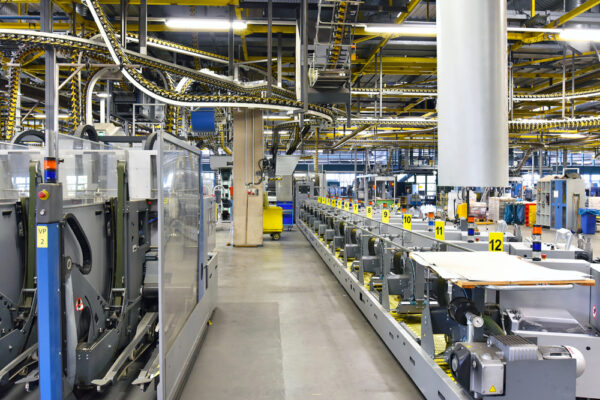
Given its importance, designing an asset naming convention should be a strategic and intentional process. Organizations typically undertake this effort when transitioning to a new CMMS, consolidating data from multiple sources, or cleaning up legacy maintenance records. Whether you’re preparing for a data import or laying the groundwork for new assets, a well-designed naming scheme ensures consistency and scalability for years to come.
When developing an asset naming convention, it’s is important to think about how your team will use the information and where the names will appear, most commonly in a CMMS. Most CMMS solutions have some or all of the following fields:
- ID or Number: A unique identifier used by the system to track the asset (required)
- Name: A short, user-friendly label for the asset
- Description: A longer, more detailed summary of the asset
In addition, a CMMS may offer dedicated fields for information like asset classification, location, and other attributes. If so, you may not need to incorporate those details into your names or numbers – unless they are especially important to your users.
As mentioned earlier, the term asset naming convention is a bit misleading. In practice, it often refers to both the name and the unique identifier (or number) used to identify your assets. The following sections offer best practices for writing descriptive asset names and creating structured asset numbers.
Writing Descriptive Asset Names
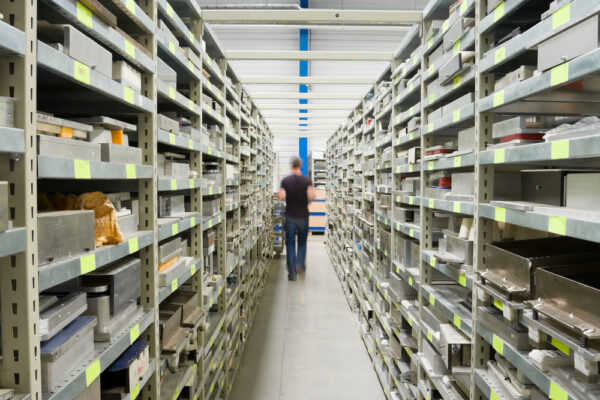
Asset names provide a human-friendly way to identify assets. Unlike asset numbers or system-generated IDs, descriptive names offer immediate recognition, helping users to understand the assets they work with.
Think of something you have a lot of – like spare parts. It would be nearly impossible to remember or recognize every item based on a number alone. Descriptive names narrow the field and reduce guesswork, especially when assets vary in size, manufacturer, or specification. While asset names may not always uniquely identify every item, they help users narrow down options.
Experts in asset management, such as Total Resource Management, recommend the following naming structures:
- Noun, Qualifier(s)
- Noun, Modifier(s), Attribute(s)
This structure describes the asset starting with the broadest category (the noun), followed by more specific descriptors.
- The Noun is the generic item name that describes what the asset is.
- The qualifier or modifier further defines the noun by specifying what kind or type the item is – often its functional category or intended use.
- The attribute adds more precise detail about the item’s appearance or physical traits. Note that in this structure, each word is capitalized and separated by a comma.
Let’s look at an example: Valve, Pressure Relief, Brass.
- Valve (noun) – what the item is
- Pressure Relief (qualifier) – its function
- Brass (attribute) – its material
FTMaintenance Select Product Expert Dave Dulak also recommends incorporating a number when managing multiple units of the same asset. For example, Valve, Pressure Relief, Brass, 001. This makes it easier to identify individual assets if the name is displayed in your CMMS without its formal number.
While descriptive asset names provide an intuitive way to identify assets, they often work hand in hand with asset numbers. A well-designed numbering system can incorporate elements from asset names or represent details in a codified format. The next section provides guidance for creating asset numbers.
Creating Asset Numbers (Unique Identifiers)
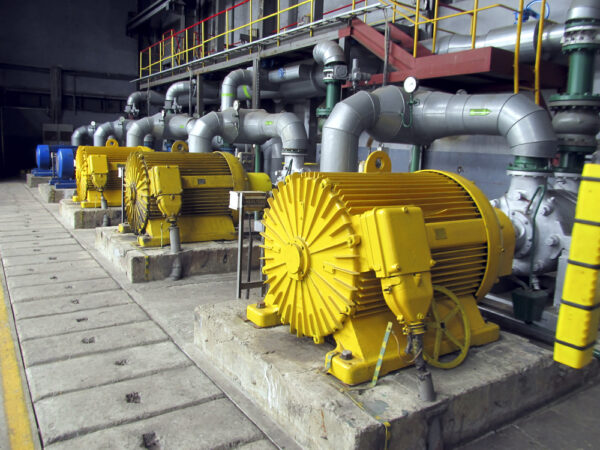
Asset numbers, also known as asset IDs, are used to uniquely identify asset records in your CMMS. While many organizations rely on system-generated or sequential numbers, this approach provides little practical value to maintenance staff or other stakeholders.
A well-structured asset numbering system, on the other hand, strengthens asset identification by reinforcing or codifying details from asset names. Together, asset names and numbers form a shared language that ensures clear communication and consistent tracking throughout day-to-day operations. To clarify, despite the term number, asset numbers can be made up of alpha-numeric characters (both letters and numbers).
There are several ways to create meaningful asset numbers, depending on your organization’s needs, existing systems, and users. The following sections present common methods for choosing or designing an asset numbering system tailored to your specific maintenance management needs.
Follow an Existing Internal Numbering Convention
Asset tracking is a shared effort between the maintenance team and other departments within your organization. In addition to the maintenance department, the finance and accounting departments are also responsible for tracking capital assets and their associated costs. These teams also rely on a well-structured numbering system to maintain consistency in financial records.
Start by reviewing how you organization’s accounting team tracks assets, and consider if their system can be applied or adapted for your needs. Even if their numbering format doesn’t fit your workflow, it’s still recommended to track the accounting number or ID in your CMMS. Doing so ensures that both departments have a common reference when referencing the same asset.
Advantages:
- Easy to Implement or Adopt: Asset names and numbers have already been assigned by an internal resource. You simply need to match them to asset records in your CMMS.
- Improved Communication: A shared naming system leads to better cross-departmental communication between maintenance, accounting, purchasing, and other teams.
Disadvantages:
- May Not Meet Maintenance Management Needs: The numbering convention may fall short of your team’s requirements if it was originally developed for accounting or another purpose.
- Possibility of Future Change: The source numbering convention may change over time, creating a mismatch between your asset records and data in other systems.
Rely on Tried-and-True Numbering Systems
While there may be pressure to develop an original numbering scheme, there’s no need to reinvent the wheel. Many proven naming conventions already exist. For example, your vendors might use a system that’s easy to adopt, or your employees may offer ideas of what worked well in their past roles.
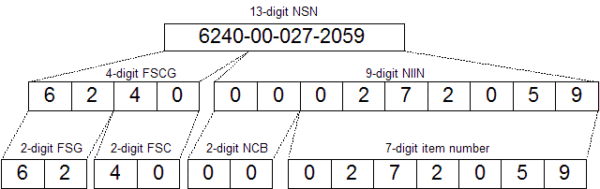
“Supply.NSN” graphic via Wikimedia Commons, released into the public domain by the creator.
One well-vetted, proven asset naming system is the United States Department of Defense’s National Stock Number (NSN) system. Often regarded as the gold standard in asset numbering, the NSN system is used by governments worldwide because it provides a standardized method to name a large number of items – as many as 6 million and counting!
A National Stock Number itself is made up of smaller subgroups, each with its own coding system. First is a 4-digit Federal Supply Classification Group (FSCG) number, comprised of the Federal Supply Group (FSG) and Federal Supply Class (FSC) numbers. Following that is the 9-digit National Item Identification Number (NIIN). The first two digits are the National Codification Bureau (NCB) numbers – effectively a “country code” that represents the nation assigning the item number. For example, the United States use “00” or “01”, while Canada uses “20” or “21”. The remaining 7 digits are unique, sequentially assigned numbers.
Of course, even widely used naming systems aren’t one-size-fits-all solutions. Basing your asset naming convention on a tried-and-true system doesn’t mean that you can’t make changes. Feel free to take the elements that work best and modify them to suit your organization’s needs. Visit the Defense Acquisition University (DAU) website for more information about the NSN.
Advantages:
- Trustworthy: The NSN system has been used by many organizations with great success, giving you the confidence that your asset naming convention will also be successful.
- Easy to Use: Established naming systems provide clear templates that simplify naming convention creation.
- Best Practices: Tried-and-true naming conventions are regarded as best practice, which may not necessarily be true with internal or custom naming systems.
Disadvantages:
- Complexity: Some naming conventions involve multiple coding layers, making it tedious to follow or apply.
- Too Large of a Scope: Systems like the NSN are designed to track millions of assets and might be too detailed for smaller organizations that could benefit from a simpler naming strategy.
Use a Custom Asset Numbering Convention
While it’s often convenient to adapt an existing numbering convention, these systems don’t always align with your workflows, terminology, or user needs. In such situations, creating your own asset numbering system gives you flexibility to make identifiers more meaningful for your team.
The complexity of your custom numbering system may depend on the structure of your CMMS. If your software lacks dedicated fields for information like location or category, you may need to encode those details into the asset number. On the other hand, if your CMMS includes robust data fields to store these details, your asset numbers can be simpler, since the system already captures that information elsewhere.
Advantages
- Flexibility: Since you are not locked into pre-defined rules, you can incorporate the information and formatting of your choice.
- Meets Your Specific Requirements: Custom naming conventions are made by the people who understand your assets and workflows best, allowing you to address the exact needs of your organization or industry.
Disadvantages
- Time to Develop: Designing a custom naming convention requires thoughtful planning. You’ll need to define consistent rules that work for your current assets while anticipating future use cases and edge scenarios.
- Longevity: A rigid or poorly-design system may become outdated or difficult to maintain. Overtime, inconsistencies may require cleanup and possible restructuring.
Custom Asset Numbering Examples
The following examples illustrate how the level of detail in asset numbers varies depending on the capabilities of your CMMS. Each approach has its pros and cons and should align with your system’s functionality and the complexity of your asset portfolio.
Example 1: Simplified Numbering with Dedicated CMMS Fields
An organization’s CMMS has dedicated input fields to store information such as asset category, location, manufacturer, and other details. The maintenance team opts for a simplified numbering scheme since the CMMS allows users to search, sort, and filter on any input field, so details like category or location do not need to be codified in the number. For this organization, the numbering convention might be AAA-###, where:
- AAA: A three-character abbreviation that identifies the type of asset
- Hyphen (-): A visual separator between encoded data
- ###: A unique identifier that distinguishes the asset from others
Following this format, CNC-001 represents one of the CNC turning centers. A second CNC machine would be CNC-002, and so on. The CMMS displays other information related to the CNC, helping users choose the specific asset in selection screens. This approach works well for organizations with a manageable number of assets, but may not scale as easily in large enterprises.
Example 2: Embedding More Detail into Asset Numbers
An organization’s CMMS has limited fields for tracking asset data. The maintenance team compensates for this by embedding location data into asset numbers. For this organization, the numbering convention might be AA-BB-CCC-###, where:
- AA: The state postal code abbreviation.
- BB: The building number where the asset is located
- CCC: A three-character abbreviation that identifies the type of asset
- ###: A unique identifier that distinguishes the asset from others
- Hyphens (-): Visual separators between encoded data
Following this format, WI-B2-CNC-003 represents one of 3 (or more) CNC turning centers located in building 2 at the Wisconsin location. While this approach helps identify assets at a glance, it is problematic for assets that change locations frequently.
Asset Naming Best Practices
Asset naming conventions do not need to be complex to be effective. The primary goal is to create a standardized system that helps your maintenance team – and others in the organization – quickly recognize assets and equipment. Follow these best practices to create names that are logical, scalable, and informative.
Be Logical
Asset names should make sense to the people using them. For example, a boiler should not be encoded as “XYZ”; instead, use familiar, instinctive abbreviations such as “BOIL” or “BLR”.
Be Consistent
Use consistent formatting and abbreviations across all assets. For example, if you abbreviate “chiller” as “CHLR”, use that abbreviation for all chillers. Similarly, use the same number formatting for all numbers. For example, use “CHLR-001”, and not “CHLR-1” or “CHLR-01”.
Be Unique
While asset names may be repeated, CMMS systems require uniqueness in numbering. Ensure each asset number is distinct from one another.
Avoid Duplicated Data
Unless it is critically important, only include information in the asset name or number that isn’t already captured in a dedicated CMMS field. Many systems provide a description field, allowing you to enter comprehensive data about your assets. These fields can be searched to locate specific assets.
Leave Room for Growth
Create naming structures that will accommodate new asset records. For example, skip numeric values (e.g., use 100, 200, 300, and so on) to leave room for sub-categories or new additions.
Prioritize the Use of Letters
Prioritize using letters over numbers, as they are easier for humans to interpret and understand. For example, use logical abbreviations: PMP for pump, AHU for air handling unit, etc.
Use a “Drill Down” Approach
Employ a hierarchical structure that starts broad and becomes more specific, allowing users to “drill down” to relevant details. This mirrors the way people naturally search for information and speeds up locating records.
Limit Name Length
Keep names concise, keeping in mind any character limitations imposed by the CMMS. Names should only include the information that’s necessary to convey to users.
Use Standard Separators
Choose a consistent separator – such as commas, hyphens, or underscores – to make names easier to search visually.
Avoid Special Characters
Avoid or limit the use of special characters (e.g., &, /, *), as they may be unsupported and can cause issues in sorting or searches.
Improve Your Asset Management Practices with FTMaintenance Select
Whether cleaning up existing maintenance data or moving to a new CMMS, analyzing your asset naming convention can reveal hidden issues in how your assets are identified. A standardized naming system increases recognition speed, improves communication, and strengthens your asset management operations.
FTMaintenance Select supports your asset management practices by providing a centralized platform to organize and track assets and equipment. By storing all asset data in a single system, it enables more accurate management of your assets, their relationships, and their maintenance needs. With powerful search, sort, and filter options, your team can better visualize your assets and quickly locate critical asset information. Request a demo of FTMaintenance Select today to see how it can elevate your asset management strategy.
Recent Comments