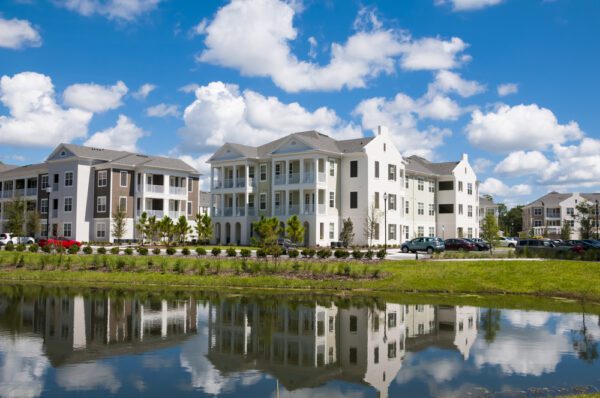
People expect the places they live, work, and interact with to be safe, functional, and well maintained, but rarely think about what it takes to keep properties that way. While much property maintenance work goes unseen, its impact is felt by everyone – from owners and property managers to tenants and guests. This article shines a light on the essential role of property maintenance in preserving real estate value and ensuring a positive experience for all who depend on well-kept properties.
What is Property Maintenance?
Property maintenance is a set of ongoing tasks and actions taken to keep properties – including buildings and their immediate surroundings – functional, safe, and in working condition. It involves maintenance activities that preserve the long-term value of the property for owners and managers, provide a comfortable and safe environment for occupants, and help attract future tenants. The term is most commonly used in reference to residential real estate and hospitality properties, where buildings and grounds are maintained for the benefit of occupants, tenants, and guests.
Building Maintenance vs. Property Maintenance
While often used interchangeably, building maintenance and property maintenance differ in scope. Building maintenance refers specifically to maintaining the physical structure itself – walls, roofs, electrical systems and plumbing – and not the land it sits on. Property maintenance includes both the building and its external features, including land, parking lots, walkways, landscaping, and other outdoor amenities.
Facility Maintenance vs. Property Maintenance
Facility maintenance is similar to property maintenance but differs in how the building is used and by whom. Facility maintenance typically refers to commercial, industrial, or institutional buildings where an owner or organization occupies and operates within the facility – and is therefore responsible for its upkeep. In contrast, property maintenance generally applies to tenant-occupied spaces, where maintenance is often handled by property management teams or third party service providers.
Why is Property Maintenance Important?
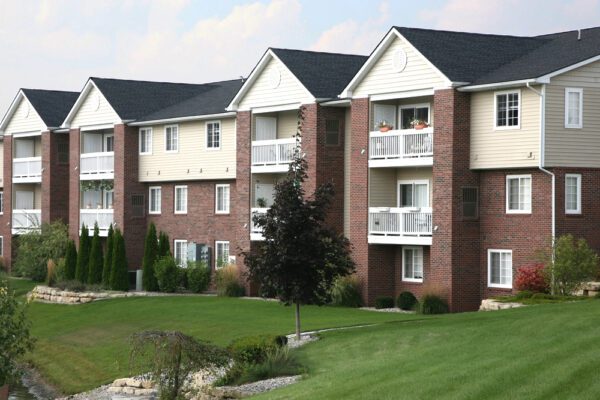
Property maintenance is a critical part of real estate and property management, benefitting everyone who interacts with a property. Below are the main objectives of property maintenance.
Maintain Habitable Living Environments
Tenants and residents have the right to live in a space that’s safe, functional, and well-maintained. This includes reliable heat, running water, working electrical systems, and a property home free from major hazards. It isn’t just best practice – in many places it’s the law.
For instance, Wisconsin state law requires landlords to keep rental homes in livable condition. This includes making necessary repairs, maintaining building systems, and ensuring the property complies with all local building and housing codes. In federally subsidized housing, the United States Department of Housing and Urban Development (HUD) enforces similar standards known as the Housing Quality Standards (HQS).
Provide Safety and Comfort
While habitability laws set the bare minimum, good property maintenance goes beyond what is required. Property owners and managers also contribute to tenant safety, comfort, and satisfaction by maintaining clean common areas, responding quickly to maintenance requests, and keeping exteriors well-maintained and attractive. This not only keeps current tenants and guests happy, but also attracts future renters and builds a positive reputation.
Protect Long-Term Property Value
Property managers want to ensure profitability, either through rental income or resale. Property maintenance ensures buildings, grounds, and amenities are kept in good condition, which helps preserve property value or justify competitive rental rates. Performing regular maintenance reduces operating costs by extending building and equipment life, preventing unexpected breakdowns, and delaying the need for major renovations.
Reduce Liabilities
Proactively addressing property maintenance helps reduce the risk of legal action, financial loss, and reputational harm. Property owners and managers can be held liable for tenant injuries caused by poorly maintained infrastructure, inadequate security, and uninhabitable living conditions. They may also face fines and penalties for violating building, health, and safety codes, and risk having insurance claims denied if property damage results from neglect.
Common Types of Property Maintenance
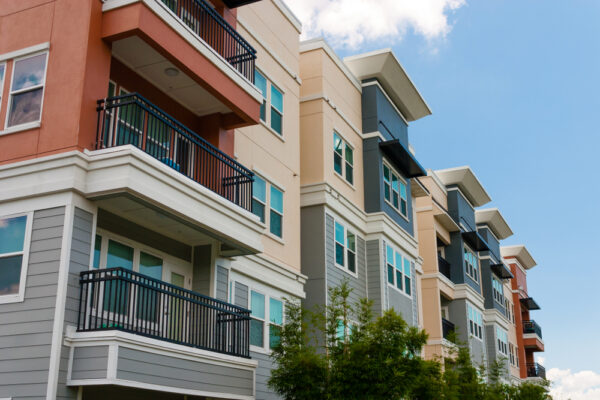
Property maintenance consists of both proactive and reactive maintenance strategies, each serving different purposes for keeping properties safe and habitable.
Preventive Maintenance
Preventive maintenance is a proactive strategy used to reduce the likelihood of failures before they happen. It typically includes inspections, replacing worn out parts, testing equipment, and addressing minor issues before they become more serious. Maintenance teams usually schedule tasks on time-based intervals, manufacturer recommendations, and equipment usage.
Corrective Maintenance
Corrective maintenance is a reactive approach performed in response to problems after they have occurred. The goal is to restore assets to working condition as quickly as possible. Property maintenance teams typically learn about these issues through maintenance requests submitted by tenants or staff. Common examples include plumbing issues, electrical failures, broken appliances, and malfunctioning HVAC systems.
Learn more about FTMaintenance Select Maintenance Request Software
Protective Maintenance
Protective maintenance is a subset of preventive maintenance that focuses on shielding exterior surfaces and outdoor equipment from environmental wear and tear. It typically involves applying paints, sealants, and coatings to building exteriors to guard against weather damage, rust, and deterioration. In property maintenance, this extends to outdoor features like patios, retaining walls, and fences, as well as protecting outdoor electrical equipment and other infrastructure through weatherproofing.
Condition-based Maintenance
Condition-based maintenance (CbM) is a proactive maintenance strategy in which maintenance tasks are triggered by an asset’s condition, rather than by strict calendar-based or time-based intervals. It typically arises from visual inspections, checklists, and routine evaluations. For example, periodic roof inspections might reveal early signs of water damage, missing shingles, clogged gutters, or other issues that can be addressed before they get worse.
Capital Improvements
While maintenance teams may not lead capital improvements, they often play a valuable supporting role. During the asset planning phase, they can provide insight about the reliability of existing assets, recurring maintenance challenges, and suggest upgrades that could reduce long-term maintenance costs.
Depending on the size and structure of the organization, maintenance teams may assist with or even carry out certain improvements, like replacing air handling units, renovating common areas, or painting. They may also work alongside contractors by preparing work areas and ensuring the safety of both workers and tenants during the project.
After upgrades are complete, the maintenance team is responsible for tracking the new assets and performing ongoing maintenance and repairs.
Learn more about asset lifecycle management.
Areas of Property Maintenance
Property maintenance covers more than just buildings – it includes all the systems, structures, and other spaces that keep a property functional, safe, and visually appealing. To understand the full scope of property maintenance, it can be broken down into three main categories: building systems, structures, and grounds.
Building Systems
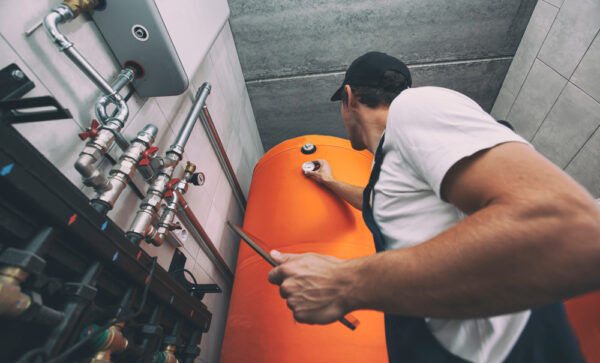
Building systems are the “hidden” components that make up a property. They are interconnected systems that ensure a property’s functionality and safety. Major building systems include:
- Electrical systems: indoor/outdoor lighting, safety systems, and backup power generators
- Plumbing systems: toilets, sinks, hot water heaters, storm drainage, fire suppression, and irrigation. In hospitality settings, this may also include commercial kitchen plumbing and grease traps
- Heating, ventilation, and air conditioning (HVAC): air handling equipment and climate control units
- Wastewater and water treatment: sewage, stormwater management, and filtration systems
- Elevators and escalators
Structures
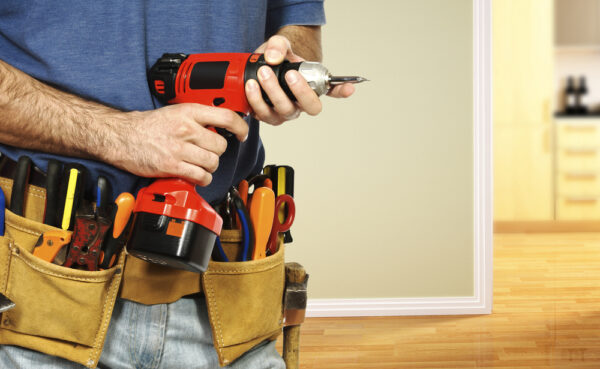
Beyond internal systems, property maintenance also extends to the spaces where people live, gather, and use, along with the physical building itself. This includes:
- Interior maintenance: cleaning, trash removal, repainting, and repairing walls, flooring, windows, and fixtures
- Exterior maintenance: siding, roofing, sidewalks, foundations, exterior lighting, and signage
- Other structures: garages, clubhouses, pools, locker rooms, storage sheds, fences, gates, and outdoor stairways
- Back-of-house areas: laundry facilities, kitchens, staff rest areas, storage facilities
Grounds
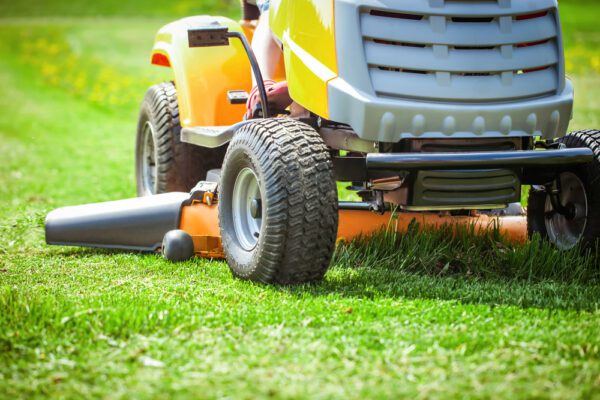
Aside from building maintenance, property maintenance also focuses on keeping the surrounding land safe, attractive, and usable. Grounds maintenance may include:
- Landscaping: mowing, weeding, seasonal planting and seasonal cleanup, pest control
- Pavement care: resurfacing, sealcoating, pothole repair, lighting, and snow and ice removal
- Perimeter elements: fences, gates, and exterior signage
- Outdoor amenities: playgrounds, water parks, sports courts, walking paths, dog parks, and even golf courses, where applicable
Who is Responsible for Property Maintenance?
Property maintenance is a shared responsibility among several roles, each contributing in different ways based on their relationship to the property.
Owners
As the legal titleholder, the owner holds ultimate responsibility for ensuring a property is well-maintained and compliant. Owners typically hire property management companies or maintenance service providers to handle day-to-day maintenance operations. While not involved in daily tasks, owners retain control by approving maintenance budgets, setting spending limits, and authorizing major repairs and capital improvements.
Property Managers
Property managers are hired by owners to oversee day-to-day property maintenance while working within an approved budget. These responsibilities include responding to tenant maintenance requests, scheduling routine maintenance and inspections, and coordinating repairs with contractors. They also ensure tenants fulfill their maintenance-related responsibilities under the lease agreement.
Maintenance Technicians
Maintenance technicians perform maintenance and repairs according to the needs of the property and as assigned by the property manager. Tasks range from completing service requests to preventive maintenance activities such as performing inspections and replacing worn parts. Their work requires technical expertise in plumbing, electrical, HVAC, and other core building systems.
Janitorial Staff
Depending on the organization, janitorial staff may help support property maintenance by handling routine cleaning and sanitation tasks. Their responsibilities often include trash removal, vacuuming, surface cleaning, disinfecting shared spaces, and occasionally cleaning up biohazards like bodily fluids. By handling these essential day-to-day responsibilities, janitorial workers allow the maintenance team to focus on more technical repairs and maintenance issues.
Tenants
Tenants are responsible for minor repairs and upkeep, outlined in their lease. This may include tasks such as changing light bulbs, keeping units safe and sanitary, and in certain instances, controlling pests. Renters may also be responsible for lawn care and snow and ice removal, depending on the type of property and lease details.
Contractors
Owners or managers bring in contractors for large-scale projects or highly-technical tasks that exceed the capability or manpower of the in-house team. They are called in to perform specialized tasks such as landscaping, elevator repair, or other tasks where having a full-time professional on staff wouldn’t be practical.
Property Maintenance Standards
Property maintenance standards provide guidance and requirements to help property owners and managers maintain safe, sanitary, and livable properties. Whether voluntary or mandated by law, following these standards supports tenant well-being and regulatory compliance.
One of the most widely recognized sets of standards is the International Property Maintenance Codes (IPMC), published by the International Code Council (ICC). The ICC outlines the IPMC’s minimum requirements for maintenance of existing buildings.
In addition to IPMC, property maintenance must also comply with a variety of other codes and standards, including:
Property Maintenance Software
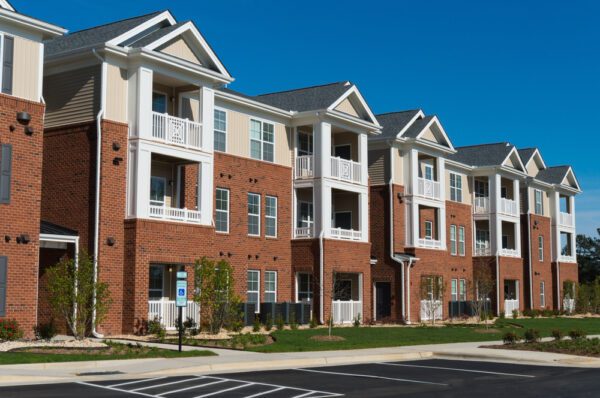
Property maintenance operations account for a significant portion of a property’s operating expenses. Given its impact on property value, tenant satisfaction, and potential liability, property maintenance deserves a tool dedicated to manage day-to-day maintenance operations. That’s why many property managers choose to track maintenance activities in a computerized maintenance management system (CMMS).
Though many property management solutions include basic work order management functionality, they often lack the depth and functionality needed to support properties with complex maintenance needs. Below are several ways a CMMS enables more effective property maintenance.
Maintenance Request Management
CMMS software provides tenants with access to an online portal to submit maintenance requests directly to the maintenance team. From the CMMS, property managers can review, prioritize, and assign maintenance tasks based on urgency. Features such as automatic notifications and status updates keep tenants in the loop about their requests, leading to higher satisfaction rates.
Learn more about FTMaintenance Select Maintenance Request Software
Asset and Equipment Management
Asset tracking features allow property maintenance managers to store detailed records about buildings, equipment, and other assets in a centralized system, providing a bird’s-eye view of all of your owned assets – and the relationships between them – making it easier to identify what assets you have, where they are located, service histories, and any upcoming maintenance needs.
Vendor Management
A CMMS helps manage the relationship with third-party service providers and parts suppliers. With vendor information stored in one place, maintenance teams can quickly coordinate repairs, source materials, and identify alternative vendors when needed.
Technician Skills and Credentials
In addition to tracking buildings and equipment, a CMMS can store important information about maintenance personnel, including their licenses, certifications, and other qualifications. This ensures work is assigned to technicians with the appropriate experience and credentials.
KPI Dashboards and Reports
Maintenance analytics give you insight into the overall performance and health of your maintenance operation. Using data-rich dashboards and reports, you can monitor key performance indicators (KPIs) related to request response times, maintenance costs, and technician productivity – often broken down by building or location.
Mobile Accessibility
Mobile accessibility is an especially valuable feature for property maintenance teams that work across large or multi-building properties. A mobile CMMS solution allows technicians to access your maintenance data from anywhere on your property. They can create and close work orders, review asset maintenance history for troubleshooting, and record preventive maintenance tasks all without returning to a desktop or office.
Protect Your Property Value with FTMaintenance Select
Property maintenance is more than routine upkeep – it’s a proactive strategy that preserves property value, ensures tenant satisfaction, and mitigates risk. From responding to tenant requests to protecting your property investments, effective maintenance plays a central role in real estate success.
FTMaintenance Select is a powerful CMMS solution designed to support the complex needs of property maintenance teams. Whether you’re managing a single rental or a wide portfolio of assets, FTMaintenance Select helps you streamline work orders, manage assets, track vendor activity, and make smarter, data-driven decisions. Request a demo today to see how FTMaintenance Select can support your property maintenance goals.
Recent Comments