When you think of a barcode system, your first thought is probably a cashier scanning items at the checkout lane at a grocery store. However, the use of barcodes is not limited to a retail environment. Many organizations use a barcode system to improve their asset and inventory tracking practices. This article provides an overview of the main components of a typical barcode system.
What is a Barcode System?
A barcode system is a network of hardware and software used to automate data collection through the use of barcodes. It consists of barcodes, barcode scanners, barcode printers and labels, and barcoding software. For maintenance management purposes, barcoding capability is usually a feature of computerized maintenance management system (CMMS) software.
There are many applications of barcoding in maintenance management, but among the most common uses are asset tagging and MRO inventory management.
Barcodes
A barcode is a representation of data in a coded format, usually in the form of parallel lines or a square of strategically spaced pixels. In simple terms, a barcode is a visual “language” that can be read by scanners and software. Barcodes are generated by barcoding software and printed onto labels using a specialized printer. Each of these components is covered elsewhere in this article.
How Do Barcodes Work
Barcodes are used to represent information that uniquely identifies an asset, such as a name or number. The combination of black and white spaces represents alphanumeric characters that follow preset rules depending on the type of barcode and barcode font being used. When scanned with a laser light from a barcode scanner, the encoded information is translated into readable data.
Types of Barcodes
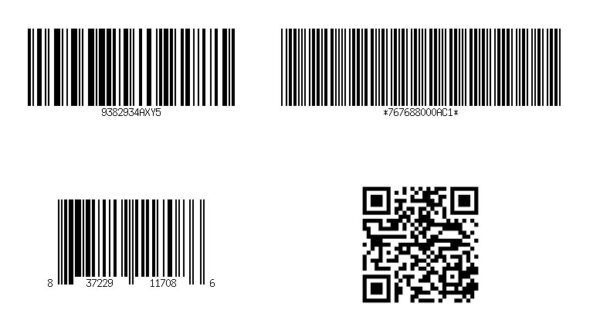
Clockwise from top left: Code 128, 1D; Code 39, 1D; Quick Response (QR) code, 2D; Universal Product Code (UPC), 1D
Barcodes are categorized as either 1-dimensional (1D) or 2-dimensional (2D). 1D barcodes are comprised of vertical lines and numbers on a single horizontal line, and are used to encode a small string of alphanumeric characters. 2D barcodes are composed using 2-dimensional symbols and shapes. Due to their increased size and dimension, 2D barcodes are used to encode larger amounts of data.
Within each barcode category are multiple different types of barcodes. Each type of barcode differs in terms of the amount of information it holds, while also considering factors such as business application, type of product, label size, and region where the business operates. Listed below are the most commonly used types of barcodes.
1-dimensional Barcodes
- Code 39: Oldest type of barcode; number can be any length that fits on the label
- Code 128: Derived from the American Standard Code for Information Exchange (ASCII) 128 character set (encoding standard for electronic communication); compact and can automatically be switched to shortened version to optimize length
- Interleaved 2 of 5: Numeric only barcode used for encoding pairs of numbers, so digits must be even
- Universal Product Code (UPC): Found on nearly every retail item, originally created for grocery stores for quick receipt printing and inventory tracking; must be 11 characters
- EAN: Subset of UPC, used by booksellers, libraries and universities for book tracking; created from 13 digit ISBN numbers
2-dimensional Barcodes
- QR: Newest type of barcode; is used to link to web pages, add contacts, scan event tickets, and much more
- PDF417: A 2D stacked linear barcode used for driver licenses and other government materials; can be linked to more than one file
- Data Matrix: A 2D square that can encode huge amounts of information in one space; used in electronics and healthcare
Barcode Scanners
A barcode scanner is an input device used to scan or read a barcode with a laser or camera. Like a keyboard, barcode scanners connect to a computer and enter encoded barcode data into a software application such as an inventory management system or CMMS. Barcode scanners can be either wired or wireless.
Wired Barcode Scanners
Wired barcode scanners are commonly used in retail settings to scan barcode labels on larger items that do not fit on the checkout lane belt. They are handheld, but have a cradle like a phone and are connected with a cord.
Wired scanners work well in small stockrooms where the cord can reach where needed, or for barcode scanning small items that are easily moved to the scanner area. Because wired scanners tether an employee to a workstation, they tend to be viewed as more cumbersome and less convenient than wireless scanners; however, they often cost less.
Wireless Barcode Scanners
Wireless barcode scanners are the most common types of barcode scanners found in an asset management and MRO inventory management environment. Like wired scanners, they are handheld and have a cradle, but are not attached with a cord. Instead, wireless scanners use radio waves to transmit data via a paired USB receiver or Bluetooth connection.
Wireless scanners are preferred over wired barcode scanners because of the mobility afforded to employees. They are easy to carry and can be used to scan assets or inventory in a wider area, though there are some limitations to their range.
Mobile Computer Scanners
The ultimate wireless scanner is a mobile computer with an integrated scanner. These devices combine the processing power of an onboard computer with the scanning functionality of wireless scanners. While wired and wireless barcode scanners must be connected to desktop computer (or laptop) in order to function, mobile computer scanners allow users to move freely and perform tasks anywhere. However, special software, docking hardware, and drivers are required for use.
Barcode Printers and Labels
In order to use barcodes, you must be able to print them. Barcode printers are specialized printers used for printing barcode labels for industrial purposes. There is a wide variety of printer options available, offering different degrees of print volume, mobility, type of printing, and printing technology. In addition, organizations must consider the type and size of barcodes to use, as well as the material used for barcode labels. They must withstand different operating environments such as hot, cold, dusty, or wet locations.
Barcode Software
Barcode software generates the 1D or 2D barcodes that get printed onto labels and read by scanners. While there are many standalone barcode software options available on the market, many do not offer the MRO inventory management capabilities required for maintenance management.
Fortunately, many CMMS solutions include barcoding functionality, so no dedicated barcode software is required. Organizations that desire to implement a barcode system are responsible for selecting compatible scanners, printers, and labels.
Barcoding with FTMaintenance Select
FTMaintenance Select barcode capability saves you time in identifying your assets and introducing a high level of accuracy into your organization’s everyday data entry activities. Leverage our consulting services to explore how you can integrate a barcode system into your existing inventory management, asset management, and work order management processes. Contact us today to learn more about the FTMaintenance Select barcode system.
Recent Comments