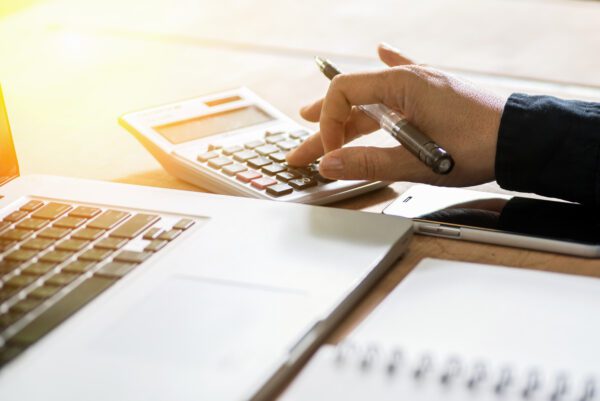
Pricing is a key factor organizations consider when evaluating computerized maintenance management system (CMMS) software. As you may have noticed during your research, CMMS vendors set their prices in various ways, making it difficult to make apples-to-apples comparisons between solutions. We’ve created this article to help you understand CMMS software pricing in order to make an informed purchasing decision about your future maintenance software.
How is CMMS Pricing Determined?
In general, CMMS pricing is determined by three factors: 1) deployment method, 2) the number of users who will access the CMMS, and 3) features.
Deployment refers to how the CMMS is delivered. Buyers have the choice between on-premise software which is installed and run locally, or cloud-based CMMS which is installed and run on vendor-owned or –leased servers. Cloud deployments are the most common.
The number of users refers to the number of people that will require a username and password to log in to the CMMS. Each of these users requires a license, with some exceptions. Depending on the system, light users such as service requesters may not require licenses. Unlimited user licenses are also available.
Features are the functional capabilities available to users. This includes all the features included in the base software, but may also extend to mobile apps or other product interfaces.
Common CMMS Software Pricing Models
The following software pricing models are commonly used by CMMS vendors.
Per User Pricing
Per user, or per seat, pricing is the most straightforward CMMS pricing model. Per user pricing is based on the number of users who are authorized to access the software. Essentially, each user who requires access to the CMMS is considered a “seat” or unit, and the price is calculated accordingly.
This pricing model is often the preferred option for businesses that require a fixed number of users to access the CMMS. It provides a predictable cost structure that is easy to understand and manage. Additionally, the per user pricing model often includes the option for quantity discounts, which is beneficial to businesses that require a large number of user licenses.
Overall, the per user pricing model provides businesses with a clear understanding of how much they will be paying based on the number of users who require access to the CMMS.
Per Feature Pricing
Per feature pricing is a type of CMMS pricing model that is based on the specific functionality that a business requires. Typically, vendors offer a basic package that includes essential features such as work order management software and asset management, with the ability to add additional features “a la carte” or individually.
This pricing model allows businesses to customize their CMMS to meet their specific needs, by only paying for the features that they require. However, it is worth noting that this can lead to increased costs, particularly if a business requires premium features that are not included in the base package.
While per feature pricing can be a flexible option, organizations should carefully consider which features they require and whether it is cost-effective to pay for them on an individual basis. It is also worth noting that this pricing model can be more complex to manage than per user pricing, particularly if multiple features are required.
Overall, per feature pricing can be a useful option for organizations that require customized functionality from their CMMS. However, careful consideration should be given to which features are required and whether this pricing model represents the best value for the money.
Per Asset Pricing
In contrast to pricing models that are based on users or features, some CMMS vendors determine their pricing based on the size of an organization. This pricing model is commonly known as per asset pricing and is based on factors such as area of a facility (in square feet), the number of facilities in which the CMMS will be utilized, the number of assets that will be managed in the CMMS, or a combination of these factors.
Per asset pricing is particularly useful for organizations that have a significant physical footprint, are asset-intensive, and require access for a large number of users. By basing the pricing on the number of assets or size of the facility, this pricing model provides cost savings opportunities for organizations with a large number of assets to manage.
Additionally, per asset pricing provides organizations with a more accurate pricing structure that aligns with their needs. Rather than paying a fixed price based on the number of users or features, per asset pricing is tailored to the specific needs of an organization. This can be particularly useful for organizations with unique requirements that cannot be met by other pricing models.
Overall, per asset pricing can provide a cost-effective and flexible pricing structure for organizations with significant physical assets. By tailoring pricing to the specific needs of an organization, this pricing model provides cost savings opportunities and a more accurate pricing structure that better aligns with business needs.
Per Work Order Pricing
While per user, per feature, and per asset pricing models are the most common in the CMMS market, there are some vendors that offer a different CMMS pricing model that may suit some organizations’ needs. This model is known as a pay-as-you-go, usage-based model, and is based on the number of work orders processed in a set time frame, usually monthly.
With this pricing model, organizations only pay for the number of work orders they process, making it ideal for those that use the CMMS inconsistently or process a small number of work orders. This model allows organizations to avoid paying for features or user licenses that they don’t need and only pay for what they use.
This CMMS pricing model can be particularly useful for businesses that experience seasonal fluctuations in work order volume, or those that operate in industries with unpredictable demand for maintenance services. By using a usage-based model, these organizations can manage their costs more effectively and adjust their usage of the CMMS accordingly.
It is worth noting, however, that this pricing model may not be the most cost-effective option for organizations with high work order volumes, as the cost can quickly add up. Additionally, some vendors may require a minimum number of work orders to be processed each month, which may not suit the needs of all organizations.
Tiered Pricing
One of the most popular ways that vendors provide pricing for their CMMS software is through a tiered pricing model. This pricing model combines per user and per feature pricing, allowing vendors to offer multiple solutions that can cater to the needs of different maintenance teams.
The tiered pricing model typically consists of several different packages, each with a different set of features and functionalities. They are structured in a tiered format, with each higher tier offering more advanced features and capabilities than the previous one.
The lowest tier typically offers a basic package with a limited set of features, such as work order management and asset tracking. As buyers move up to the higher tiers, they gain access to more advanced features and functionality, such as predictive maintenance, mobile app access, and real-time data analysis.
Pricing for each tier is usually based on the number of users that will access the system, and the number of features that are included. The lowest tier comes at the lowest price, while higher tiers with more advanced features come at a higher cost.
The advantage of tiered pricing is that it allows buyers to choose the package that best fits their specific needs and budget. Users can start with at the lowest tier solution and then upgrade to a higher tier as their needs grow, rather than having to purchase an entirely new system.
Additionally, the tiered CMMS pricing model provides more transparency in pricing, as users can easily see what features are included in each tier and compare the costs. This helps organizations make more informed purchase decisions and avoid overpaying for features they may not need.
Other Costs to Consider
The cost of a CMMS is more than the price of the software. Below are some other costs to consider when evaluating potential CMMS solutions.
Software Setup
Software setup costs are affected by your chosen deployment method, and include anything required to get your software into the hands of your team. For on-premise deployments, these costs include hardware, software, and IT infrastructure required to support the CMMS. In some cases, vendor assistance may be needed to ensure a proper installation.
Cloud-based solutions are accessed over the internet and do not require installation. However, you will need to purchase mobile devices if you expect your team to access the CMMS from the field.
Further Reading: How to Choose Mobile Devices for Your Maintenance Team
Training
CMMS training options and pricing vary by vendor. While many vendors include introductory training with initial purchase, some require the purchase of specialized onboarding training sessions. User training may also be available through user manuals, recorded videos, live webinars, or online knowledge bases. In-person, onsite training may be available or purchased separately or only available with the highest tier CMMS package.
Besides startup training, also consider the cost of ongoing user training. Ongoing training helps train new hires on the CMMS and provides a refresher for veteran employees. Training may also be necessary when you expand use of the system, such as using a mobile CMMS app alongside your cloud CMMS software.
Support
In most cases, vendors offer basic online or email support as part of a CMMS purchase. However, there may be additional charges for phone support or priority support. Organizations with a cloud-hosted solution may also be required to pay a separate hosting fee.
Maintenance
Ongoing CMMS maintenance costs include product updates, patches, and software upgrades. These costs are usually included with cloud-hosted subscriptions. Organizations with an on-premise installation may be required to pay for new software versions.
Explore FTMaintenance Select Purchase Options
Comparing CMMS pricing between vendors can be a challenge when pricing is presented in various ways. FTMaintenance Select offers flexible CMMS purchase options with both on-premise and cloud-hosted options. Contact our sales team today to learn more about FTMaintenance Select.
Recent Comments