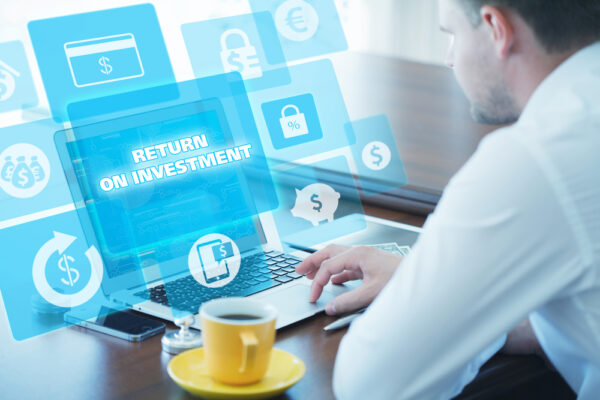
When upper management sets a goal like reducing maintenance costs, it’s up to maintenance leaders to figure out how to make it happen. That often means taking a hard look at current operations and identifying ways to be more efficient, proactive, and accountable.
While there are many ways to control maintenance costs, one of the most effective solutions is a computerized maintenance management system (CMMS). But before you can move forward, you’ll likely need to build a business case that shows how the investment will pay off – and when.
In this article, you’ll learn how to calculate the return on investment (ROI) for a CMMS by estimating current maintenance costs, projecting the value a CMMS can deliver, and determining how long it will take to recover your investment.
Understanding CMMS ROI
CMMS ROI measures how much value you gain from CMMS software relative to the cost of investment within a set timeframe. Although ROI is often used after a purchase to assess cost-effectiveness, it can also be used during the buying process as a forecasting tool to project potential value and justify the purchase.
By calculating project ROI, you can build a strong business case for investing in a CMMS and demonstrate to executives how it will reduce maintenance costs.
CMMS ROI Formula

To calculate CMMS ROI, compare the cost of implementing the software against its value over a given period. The most common way to calculate ROI is subtracting the CMMS cost from its potential value, then dividing by the CMMS cost. To get the most accurate ROI estimation, you must know:
- CMMS Cost: The purchase price of the software, including any additional costs for implementation, training and customer support, or hardware
- Potential CMMS Value: The projected cost savings across all areas of your maintenance operations
- Timeframe: The period over which benefits are measured – often 1, 5, or 10 years, as determined by upper management.
To calculate CMMS ROI, you’ll need to estimate both the cost of the system and the value it provides. The sections below explain how to gather the numbers needed to plug into the ROI formula.
Determining CMMS Cost
When estimating your CMMS investment, be sure to account for both direct and indirect costs.
The direct cost of a CMMS is the purchase price of the system, including licenses and any supporting infrastructure or services required to get your team up and running. Indirect costs are related to your specific implementation needs and may be impacted by your organization, industry, and deployment requirements. These can include:
- Implementation services such as installation, consulting, data importation, or system integration
- User training
- Customer support contracts
- Hardware like mobile devices, barcode systems, or servers (for CMMS deployed on-premise)
- Software such as operating systems or web browsers
- Software validation (especially in regulated industries)
For example, if you plan to give technicians access to work orders while in the field, you may need to purchase mobile devices or upgrade your internet service. Costs like these aren’t included in vendor quotes, but they’re essential to determining an accurate CMMS ROI.
Further Reading: 10 Things to Consider When Searching for CMMS Software
Determining CMMS Value
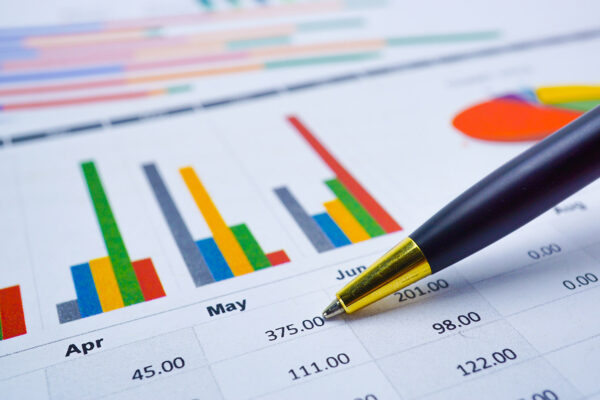
To estimate the potential value a CMMS can deliver, you have to understand what you’re currently spending – and where – and how the software will help you reduce those costs. In most cases, the value of a CMMS comes from eliminating inefficiencies like saving time, preventing unplanned downtime, and reducing unnecessary spending.
Where a CMMS Adds Value
A CMMS creates savings across several areas of your maintenance operations. Common areas of impact include:
- Administrative Tasks: Less time generating and processing work orders, managing incoming service requests, and scheduling recurring tasks
- Inventory: Fewer rush orders, reduced excess stock, better part availability, and improved tracking of locations and quantities
- Labor Management: Faster response times, less manual data entry, improved oversight, and more time for hands-on maintenance work
- Equipment Reliability: Fewer unplanned breakdowns, better failure tracking and root cause analysis, and greater visibility into asset condition and performance
- Reporting and Compliance: Automated KPI tracking, recordkeeping, and documentation to support maintenance audits and regulatory compliance
Understanding where a CMMS adds value is only half the equation. You also need to estimate your current maintenance costs in each of those categories to determine how much you could save.
How to Estimate Current Maintenance Costs
Organizations that formally track maintenance costs may have data readily available through their accounting system or enterprise resource planning (ERP) software. For example, the accounting team may be able to provide overall maintenance, labor, and material costs. The procurement team may provide information about MRO inventory purchases. Historical work orders can also be used to estimate maintenance costs, assuming that such information is documented.
If exact figures aren’t available, thinking of costs in terms of time can be a useful substitute. Ask questions like:
- How many hours of emergency maintenance do we experience per week, month, or year?
- How many hours of lost production time do we average weekly, monthly, or annually?
- How much time is spent creating and closing work orders each week, month, or year?
Then, assign a cost to each unit of time.
For example, if your technicians average 10 hours per week on emergency maintenance and the average labor rate is $35 per hour, that’s $350 per week – or over $18,000 per year. That’s just the labor cost, not including any overtime, lost production, or other consequences.
You can repeat this exercise across multiple areas or your operations to build a complete picture of your current maintenance spend.
Be sure to calculate all costs using the same timeframe you plan to use for your CMMS ROI calculation. For example, if you’re calculating ROI over a 1-year period, multiply your average monthly cost by 12 – or your weekly cost by 52 – to estimate annual totals. This ensures that your cost and value estimates are consistent, making your final ROI calculation meaningful and defensible.
Projecting CMMS Savings
Once you’ve estimated your current maintenance costs, the next step is to project how a CMMS can reduce them. To do that, look at your baseline numbers and apply a reasonable percentage reduction based on process improvements or efficiency gains.
Let’s revisit the earlier emergency maintenance example:
If your team currently spends 10 hours per week on emergency repairs at a labor rate of $35 per hour, that’s $18,200 per year. If you project that a CMMS could reduce that time by 20% (from 10 hours to 8 hours per week), that’s a savings of $3,640 per year in labor costs alone.
This same method can be applied anywhere a CMMS adds value. The more accurate your current cost estimates, the more realistic your projected savings will be.
What Percentages Should You Use?
Industry reports and vendor case studies often suggest that CMMS users can achieve cost savings between 20%-50% across various maintenance management areas. While these figures are encouraging, they represent best-case scenarios and may not reflect your organization’s current maturity, processes, or readiness for change.
We encourage you to treat these benchmarks as high-end estimates, not guaranteed results. Instead of taking percentages at face value, focus on making realistic projections based on your organization’s goals and known inefficiencies. Here are a few data points to consider:
- A Plant Engineering example shows gradual cost savings of 2%, 4%, and 7% over three years based on growing CMMS adoption and process improvements.
- A Reliable Plant article estimates organizations can save 12% – 18% by shifting from reactive to preventive maintenance.
- A Maintenance World article suggests successful CMMS implementations may reduce overall maintenance costs by up to 40%, and inventory valuation by up to 30%.
Because these numbers vary widely, consider starting with conservative estimates. You might estimate 5% – 20% savings in high-impact areas like labor, unplanned downtime, inventory, or administrative overhead. As noted in our example earlier, reducing emergency maintenance by just 2 hours per week led to a 20% reduction in labor costs.
If you are still unsure where to start, identify one or two high-cost areas in your current operation and apply modest reduction percentages. Even small improvements can lead to significant ROI when scaled across your entire operation over time.
Putting it All Together: 5-Year CMMS ROI Example
Once you’ve estimated your maintenance costs and projected the value a CMMS can deliver, you can calculate your return on investment using the formula provided earlier:
CMMS ROI = (CMMS Value – CMMS Cost) ÷ CMMS Cost
Let’s walk through a realistic example using the following assumptions:
- Upper management requests an ROI projection over a 5-year period
- The organization subscribes to a cloud-hosted CMMS for 5 users
- Licenses are $50 per user, per month – totaling $3,000 per year
- Initial annual savings = $5,000, broken down as follows:
- $3,640 in labor savings, based on 2 fewer emergency maintenance hours per week
- $800 in inventory savings, based on fewer rush orders and better inventory control
- $560 in administrative time, based on improved work order processing
- Savings increase modestly over time as the maintenance team becomes more proficient in using the CMMS
In this example, ROI is calculated cumulatively over five years – meaning total costs and savings are tallied each year before the ROI formula is applied. Note that for simplicity, this example assumes annual costs remain constant over the 5-year period.
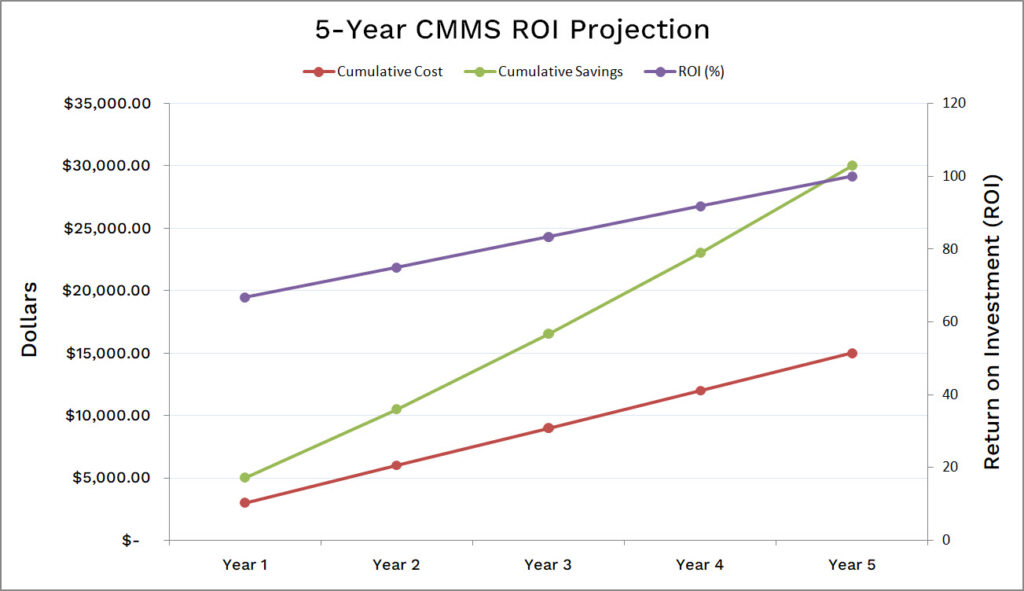
Year |
Annual Cost |
Annual Savings |
Cumulative Cost |
Cumulative Savings |
ROI Calculation |
ROI |
1 |
$3,000 |
$5,000 |
$3,000 |
$5,000 |
($5,000 – $3,000) / $3,000 |
66.7% |
2 |
$3,000 |
$5,500 |
$6,000 |
$10,500 |
($10,500 – $6,000) / $6,000 |
75% |
3 |
$3,000 |
$6,000 |
$9,000 |
$16,500 |
($16,500 – $9,000) / $9,000 |
83.3% |
4 |
$3,000 |
$6,500 |
$12,000 |
$23,000 |
($23,000 – $12,000) / $12,000 |
91.7% |
5 |
$3,000 |
$7,000 |
$15,000 |
$30,000 |
($30,000 – $15,000) / $15,000 |
100% |
After 5 years, the CMMS not only pays for itself but delivers an additional $15,000 in savings, resulting in a 100% return on investment.
How to Interpret CMMS ROI
CMMS ROI is a simple measurement of the software’s value to your organization in terms of cost savings. A positive ROI (greater than 0) means the system is generating benefits and saving money. A negative ROI (less than 0) means the system has not yet paid for itself – but that doesn’t mean it won’t.
It’s common to see a negative ROI in the first year due to upfront costs, implementation timeline, and the time it takes for teams to fully adopt and use the system effectively. That’s why it’s important to evaluate ROI over multiple years, giving the system time to demonstrate its full value.
Determining the Payback Period

In addition to projecting ROI, upper management will want to know how quickly they will recoup their investment, known as the payback period. To calculate the payback period, divide the CMMS cost by the cost savings.
In our example from earlier, the investment was returned in Year 1. Let’s calculate that payback period mathematically using the formula provided:
Payback Period = $3,000 ÷ $5,000 = 0.6 years (7.2 months)
In Year 1, the CMMS is projected to pay for itself within 7.2 months and deliver an additional $2,000 in cost savings.
Achieve a Quick Payback with FTMaintenance Select
While individual results will vary, the payback period with FTMaintenance Select maintenance management software can be as short as 4 months! We offer affordable subscription licensing that eliminates the large, upfront costs of other pricing structures. FasTrak further expedites the payback period through complimentary CMMS implementation services and webinar-based user training .
As a customer, you have unlimited access to our CMMS customer support to answer your questions and assist you in getting comfortable with FTMaintenance Select. As you begin to master FTMaintenance Select and maximize the use of our powerful CMMS features , the payback period becomes a lot shorter. |
Lower Maintenance Costs with FTMaintenance Select
When tasked with finding ways to reduce your operational costs, look no further than FTMaintenance Select. Our CMMS software digitizes your maintenance tracking and streamlines your day-to-day administrative tasks by automating work orders, asset tracking, preventive maintenance scheduling, inventory control, reporting, and more. Request a demo today to see how FTMaintenance Select reduces maintenance costs and improves efficiency.
Recent Comments