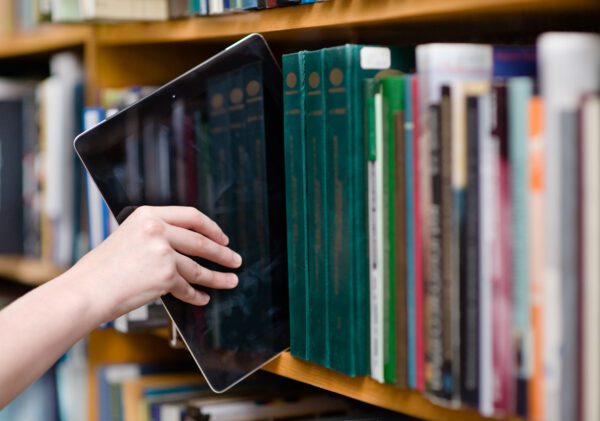
Our health and well-being depends on the safety, effectiveness, and security of products we consume and use on our bodies. To protect public health, the United States Food and Drug Administration (FDA) imposes strict oversight on food and beverage, pharmaceutical, and related industries (like medical devices, cosmetics, and tobacco products). The FDA Title 21 CFR Part 11 standard is of special interest to maintenance teams in certain FDA-regulated industries. This article provides an overview of how computerized maintenance management system (CMMS) software can help you achieve compliance with 21 CFR Part 11 requirements.
What is Title 21 CFR Part 11?
The Code of Federal Regulation (CFR) Title 21 lists all federal regulations for organizations operating in the food and drug industry. Of these regulations, the ones most apparent to maintenance teams are Good Manufacturing Practices (GMP) and Title 21 CFR Part 11, which covers requirements for electronic records and electronic signatures.
Why is the 21 CFR Part 11 Standard Necessary?
Traditionally, many maintenance departments relied on manual, paper-based systems to plan and track maintenance work. Like today, the FDA maintained regulations and requirements for these paper records. However, as one can imagine, creating, collecting, storing, and maintaining paper documents requires a lot of time, effort, and physical space. Computerization solved many of these issues.
As computing and digital archiving technology advanced in the 1980s and 1990s, organizations migrated away from manual recordkeeping towards computerized systems. Although the digitization of data made exchanging, searching, and retrieving data easier, the FDA had concerns about the reliability, validity, and authenticity of digital records, compared to paper-based records. Essentially, the FDA felt that digital records were too easy to falsify, which led to the development and implementation of the 21 CFR Part 11 standard in 1997.
21 CFR Part 11 regulations are necessary to protect public health and safety by ensuring that FDA-regulated industries conduct business in a trustworthy, transparent manner. Specifically, this standard sets the criteria for which electronic records and signatures can be accepted as equivalent to their handwritten counterparts of the past. This is especially important today when it is common for bad actors to manipulate and fraudulently modify digital data.
Read Also: A Brief History of CMMS Software
What are 21 CFR Part 11 Requirements?
FDA 21 CFR Part 11 requirements cover two main topics: electronic records and electronic signatures. We provide an overview of these requirements below.
Disclaimer: While we make every effort to keep information up to date and accurate, compliance requirements are subject to change without our knowledge. Your organization holds responsibility for verifying any information discussed in this article with official sources before applying it to your organization. Please review the disclaimer in our Terms and Conditions for more information. |
Electronic Recordkeeping
21 CFR Part 11 states that people who create records in a computer system, such as a CMMS, must create procedures and controls to ensure the authenticity, integrity, and confidentiality of electronic records. Electronic records are defined as “any combination of text, graphics, data, audio, pictorial, or other information representation in digital form that is created, modified, maintained, archived, retrieved, or distributed by a computer system.”
Maintenance teams must do the following to comply with electronic record requirements:
- Validate CMMS software and other recordkeeping systems
- Generate copies of records in human readable and electronic form
- Protect records to enable accuracy and easy retrieval
- Limit system access to authorized users
- Create and maintain an audit trail of changes to maintenance records
- Ensure the system enforces required workflows
- Ensure only authorized users access and use the system
- Verify the identity of users
- Train users to perform assigned tasks
- Document and follow 21 CFR Part 11-compliant policies
- Control distribution of, access to, and use of documentation about the CMMS
Electronic Signatures
The 21 CFR Part 11 standard defines an electronic signature as “a computer data compilation of any symbol or series of symbols executed, adopted, or authorized by an individual to be the legally binding equivalent of the individual’s handwritten signature”. Electronic signatures must contain the following information to be considered equivalent to the individual’s handwritten signature:
- The printed name of the signer
- The date and time of the signature
- The meaning associated with the signature, such as review, approval, or responsibility
In addition, electronic signatures are required to be:
- Unique to one individual and not reused or reassigned to anyone else
- Assigned only to an individual whose identity has been verified
- Certified by the signer that the signature is intended to be the legally binding equivalent as their handwritten signature
- Comprised of 2 distinct identifiers, such as a username and password
- Used only by their genuine owner
- Protected from misuse
21 CFR Part 11 also outlines requirements for controlling the security and integrity of usernames and passwords, though they are not covered in this article. Refer to the CFR 21 Part 11 documentation for more information.
CMMS and 21 CFR Part 11 Compliance
Many buyers include FDA compliance as a requirement of their future CMMS system. It is important to note, however, that a CMMS cannot be compliant in and of itself because compliance is related to how the CMMS is used.
A CMMS can help meet 21 CFR Part 11 requirements by providing an electronic system for managing maintenance activities and generating electronic records that are compliant with the regulation. Here are some ways in which a CMMS helps with compliance:
Electronic Records Management
CMMS software allows maintenance departments to manage their tasks electronically, including generating electronic records such as work orders, maintenance schedules, and equipment calibration reports. These electronic records can be managed and stored in compliance with 21 CFR Part 11 requirements, such as maintaining accurate, complete records and ensuring that records are trustworthy and reliable.
Electronic Signatures
A CMMS allows for electronic signatures to be used for approvals and sign-offs, which are necessary for maintenance activities. It can provide the necessary control to ensure compliance with 21 CFR Part 11 requirements, such as being unique to the signer, being secure, and being linked to an electronic record.
Access Controls
CMMS software provides access controls that limit access to electronic records and electronic signatures to authorized personnel only. This helps ensure that only authorized individuals create, modify, or delete electronic records and signatures, and that access to these records is tracked and audited.
Validation
Validating a CMMS ensures that it meets the requirements of 21 CFR Part 11, such as being accurate, reliable, and secure. The validation process ensures that the system is designed and operating in a manner compliant with FDA requirements.
Training
Vendor-provided CMMS training ensures that maintenance employees are able to perform their assigned tasks, demonstrate day-to-day responsibilities to auditors, and generate the documentation necessary to meet 21 CFR Part 11 requirements.
Meet FDA Requirements with FTMaintenance Select
Meeting regulatory requirements is an ongoing challenge given the number of regulations manufacturers must follow, FDA or otherwise. Some organizations may think they are in compliance with 21 CFR Part 11, only to later find out that they are not. FTMaintenance Select helps regulated manufacturers meet FDA requirements by providing a single platform for documenting, tracking, and managing maintenance records and activities. Request your demo of FTMaintenance Select today.
Recent Comments