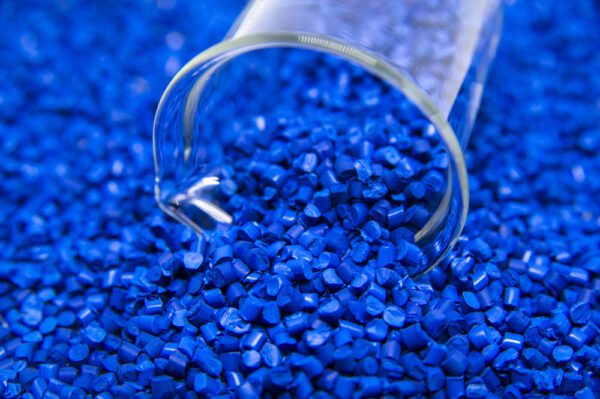
Key Takeaways
- The high demand for plastic products requires organizations to invest in modern maintenance strategies and technologies.
- The plastics industry at large faces numerous maintenance management challenges that threaten production timelines and quotes, product quality, and overall profitability.
- CMMS software, like FTMaintenance Select, helps plastics manufacturers effectively manage assets, maintenance planning and scheduling, and more.
Plastic products play a critical role in our daily lives, ranging from simple household items like toothbrushes and combs, to cutting-edge technology like 3D printing. With an estimated global market value of $712 billion (USD), the high demand for plastic products highlights their importance across various consumer and industrial markets.
To keep pace with current demand and expected growth, plastics manufacturers must invest in effective maintenance strategies and technologies such as computerized maintenance management system (CMMS) software. In this article, we will explore maintenance management challenges in the plastics industry and how a CMMS helps ensure efficient maintenance operations.
Common Maintenance Management Challenges in Plastic Manufacturing
Maintenance management is a critical component of plastics manufacturing, ensuring that equipment remains productive and profitable. However, there are several maintenance challenges that characterize the plastics industry. The sections below discuss some of the most common.
Mold Maintenance
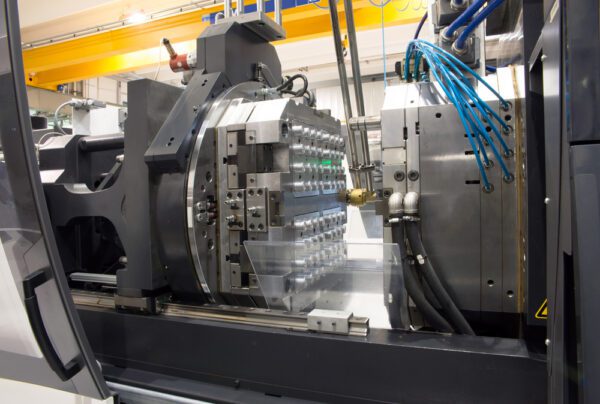
Maintaining injection molds is challenging due to their strict durability requirements and the precision of care needed to manage them effectively. These molds can be incredibly costly, often $80,000 or more, in addition to the cost of the injection molding machines themselves. Organizations must minimize mold wear and tear through targeted maintenance while working within the constraints of the production schedule and tool and die team.
Coordination with the Tool and Die Team
Coordination with the tool and die team adds another layer of complexity to maintenance in plastics manufacturing. The tool and die team is responsible for designing, building, and repairing the molds, and has specialized knowledge and skills critical for maintaining production quality. The overlap in responsibilities between the general maintenance team and tool and die team often leads to challenges in balancing competing priorities and coordinating access to maintenance resources.
Further, miscommunication between maintenance and the tool and die teams may influence the production team’s operations. If maintenance tasks are scheduled during critical production runs or repairs aren’t completed on time, there may be unnecessary downtime, higher maintenance costs, or quality issues.
Quality Control
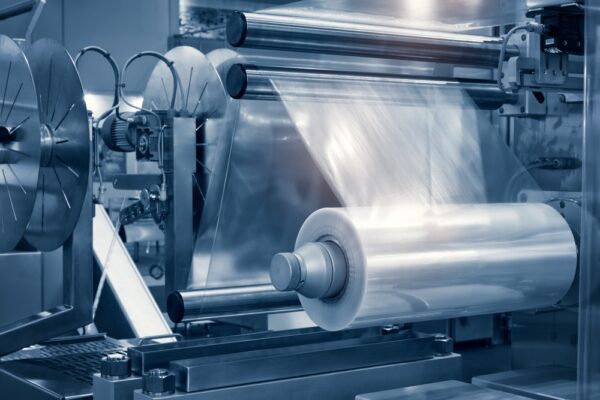
Given the high volume of products produced in plastics manufacturing, even minor equipment issues can lead to significant quality control issues. The maintenance team plays a critical role in ensuring plastic products meet stringent requirements and customer expectations.
Equipment must be kept in good working condition to eliminate defects such as surface imperfections, warping, cracking, or other inaccuracies. This requires the maintenance team to implement process control measures that include regular calibrations, condition monitoring, and preventive maintenance, which is challenging with limited resources.
Maintaining consistent quality control also becomes difficult when investigating the origin of product defects. Conducting thorough root cause analysis (RCA) is essential, but can be complex, time-consuming, and must be balanced against other immediate needs.
Environmental Factors
Environmental conditions within the plastics manufacturing facility also pose significant maintenance challenges. The high temperatures and pressures from plastic molding and extrusion processes put considerable wear on equipment, increasing the risk of failure. Avoiding these outcomes requires tight control of asset lifecycles and maintenance practices to ensure optimal performance.
Depending on your geographic location, humidity may also play a role in equipment maintenance. Excessive moisture can be absorbed by plastic materials and result in defects. Moisture that sits on equipment surfaces can corrode molds and metal components, compromising their integrity. Maintenance teams must take measures to control the temperature and humidity levels in manufacturing spaces.
Additionally, equipment is vulnerable to damage from fine plastic particles created during production. These particulates can enter machinery, causing abrasions and damaging sensitive components. While machine operators typically handle routine cleanings, maintenance teams are responsible for disassembly and deep cleaning during scheduled downtime periods.
Communication Between Maintenance and Production
Just as in other manufacturing environments, the degree of communication between maintenance and production teams can present considerable challenges. Production teams expect equipment to run at peak performance and support smooth, continuous operation in order to meet production goals and deadlines. The maintenance team is often blamed if equipment fails or experiences unplanned downtime.
On the other hand, maintenance teams can struggle to gain access to equipment for repairs. Tight production schedules leave small windows open for maintenance, and any downtime can be seen as jeopardizing production quotas. This lack of access makes it difficult to perform necessary preventive maintenance, leading to the risk of more sever breakdowns and extended downtime.
How a CMMS Helps Plastics Manufacturers Overcome Common Maintenance Challenges
Overcoming the maintenance challenges of plastics manufacturing requires a robust maintenance strategy. Computerized maintenance management system (CMMS) software provides the tools needed to meet these challenges head-on and better manage your maintenance operations. Below are some ways that a CMMS benefits the plastics industry.
Comprehensive Asset Tracking
A CMMS provides robust asset management features essential for tracking molds and plastic manufacturing equipment. It allows you to keep detailed records on all maintenance assets, including their specification, condition, availability, usage, and maintenance history. Using this information, you can manage asset lifecycles more effectively and ensure each piece of equipment receives the attention it needs.
Improved Maintenance Planning and Scheduling
In industries with high production volumes like plastics manufacturing, time is money. The consequences of downtime make reactive maintenance strategies unsustainable. The maintenance planning and scheduling features of a CMMS empower you to be more proactive about maintenance management.
CMMS software allows you to create a master preventive maintenance plan for all of your production assets, ensuring that routine maintenance is performed on time. Tasks lists allow you to define exactly what needs to be done, what materials and supplies should be used, and approximately how long routine tasks should take, leading to more consistent, quality maintenance. Work orders can then be triggered using time-based or runtime-based intervals, ensuring maintenance occurs when needed.
Some CMMS systems take proactive maintenance a step further and connect with condition-monitoring sensors. This integration supports advanced maintenance strategies like condition-based maintenance (CbM), which triggers work orders based on real-time equipment conditions, and predictive maintenance (PdM) which forecasts when equipment is expected to fail. These strategies allow you to perform maintenance only when it is needed, unlike with time-based maintenance practices.
Better Communication and Collaboration
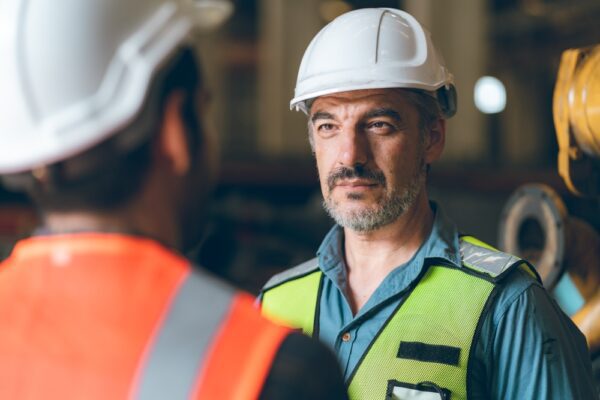
Successful maintenance management in the plastics industry relies on effective communication and collaboration between the maintenance, tool and die, and productions teams. A CMMS ensures that the general maintenance team and tool and die team have access to the same maintenance information about production equipment and can work together to prioritize repairs and coordinate resources.
CMMS solutions also include a work request portal that allows non-maintenance employees to submit service requests directly to the maintenance team. With this feature, the production team can submit requests, check request status, and be automatically notified when requests change status or are completed. This level of transparency makes everyone aware of when maintenance will occur and creates a more collaborative relationship between maintenance and production.
Enhanced Failure Analysis
Using a maintenance tracking system enables you to leverage historical maintenance data in order to diagnose why equipment failed. CMMS solutions automatically create a service history for each asset, providing you with a wealth of data that can be used to identify failure trends, track reliability following repairs, and generate maintenance management reports that reveal key insights about asset performance. This allows you to move beyond treating symptoms and address the root causes of breakdowns, thereby preventing the likelihood of the problem recurring.
Read Also: What is a Failure Code?, What is a Cause Code?, and What is a Remedy Code?
Stay In Production with FTMaintenance Select
The plastics manufacturing industry faces many maintenance management challenges that significantly impact production, product quality, and overall profitability. Given the importance of plastics in our lives, organizations that fail to tackle these challenges may find it difficult to maintain consistent production.
Now is the time to modernize your maintenance operations and invest in a computerized maintenance management system (CMMS) like FTMaintenance Select. FTMaintenance Select provides robust tools for managing assets, inventory, preventive maintenance, and work requests. Leveraging this platform, you can implement proactive maintenance strategies that will reduce downtime, ensure consistent production, and set you up for long-term success. Request a demo today to learn more.
Read More about FTMainenance Select benefits for the plastics industry
Recent Comments