Every industrial organization relies on well-maintained assets to keep their business going. Maintenance management is an important, yet seldom discussed, aspect of managing a company. People unfamiliar with working in industrial environments may not understand what is meant by maintenance management. In this article, we explore many common questions surrounding maintenance management.
What is Maintenance Management?
Maintenance management is an orderly process to control the maintenance resources and activities required to preserve assets at, or repair them to, an acceptable working order. While you may interpret this definition of maintenance management as simply meaning “fixing things,” that would be an oversimplification. There is a lot more to maintenance management than most people realize. Since much of an organization’s money is tied up in equipment and facilities, important decisions are made regarding time, people, and money.
Why is Maintenance Management Important?
Maintenance directly impacts the long-term success of an organization. Assets that are poorly maintained experience frequent, unexpected downtime, and cause a ripple effect. Instability, inconsistent product quality, stopped production, and high operational costs jeopardize an organization’s profitability and longevity.
When done properly, maintenance management keeps assets in optimum operating condition. Less disruption in production or service leads to efficient operations, increases quality, and improves productivity. In addition, maintenance management lowers operational costs, protects the organization from liability, and improves environmental and personal safety.
Further Reading: 5 Reasons Maintenance Management is Important
Objectives of Maintenance Management
All forms of maintenance management share similar objectives no matter the industry, plant, or product or service offered. The following are some objectives of maintenance management:
- Minimizing asset failure and downtime
- Extending asset life
- Planning maintenance work
- Cost control and budgeting
- Improving product quality
- Developing improved policies, procedures, and standards
- Complying with regulations
- Ensuring safety of personnel
As you can see, each of these objectives is closely tied to one another, and is crucial to the success of the organization. We cover the maintenance management objectives listed above in more detail in our article, 8 Maintenance Management Objectives.
Components of Maintenance Management
Maintenance management is made up of many key functions. Each of these functions must be managed in and of itself to improve the maintenance process. Listed below are the components of maintenance management.
Work Order Management
Work orders are the primary channel of communication for maintenance work. Work order management is the system that defines how work orders are processed and completed. It boils down to how the maintenance department makes sure that work gets done accurately and on time. This includes rule setting for work order creation, prioritization, scheduling, assignment, distribution, execution, documentation, and closure.
Read more about the work order management process.
Asset Management
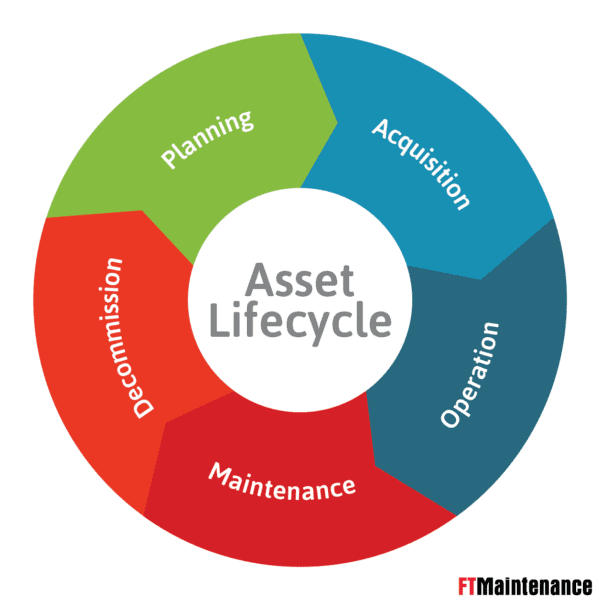
Asset Lifecycle Process
In an industrial setting, asset management seeks to maximize the value of fixed assets throughout their lifecycle. Maintenance is only one aspect of asset management, which also includes planning, acquisition, operation, and decommissioning.
For its part, maintenance management helps extend an asset’s useable life by coordinating the resources needed to keep it in operating condition. This includes monitoring an asset’s condition, knowing its performance specifications, applying effective maintenance strategies, and tracking maintenance costs. Based on these factors, an organization can determine whether it’s better to repair or replace the asset.
Facility Management
Like asset management, facility management encompasses a range of functions and activities, of which maintenance management is a part. Facility management coordinates physical workplaces, people, and support services to support business goals. This includes hard facilities management services relating to the physical structure of the building, and soft facilities management services related to people.
Maintenance management contributes in a number of ways. During everyday operations, maintenance resolves unexpected issues. Regular inspections of a building’s HVAC, electrical, plumbing, and other systems help identify longer-term maintenance needs. Additionally, maintenance management functions keep the organization up-to-date on environmental and health and safety regulations.
Read More about Facility Management: What is Facility Management?
MRO Inventory Management
Another component of maintenance management is the management of maintenance, repair, and operations (MRO) inventory. This type of inventory includes items such as chemicals and cleaners, tools, safety equipment, personal protective equipment, and other consumables. Managing MRO inventory involves procuring, storing, using, and replenishing stock at a low cost. The main functions of MRO inventory management are:
- Identification: Identifying what MRO items the organization uses and their specifications.
- Location: Creating an organized system that allows team members to find items quickly
- Procurement: Acquiring MRO items needed for maintenance work.
- Inventory Control: Ensuring the right stock is available at the right place at the right time.
Explore these concepts in detail in our article, What is MRO Inventory Management?
Maintenance Planning and Scheduling
Maintenance planning and scheduling is the cornerstones of effective maintenance management. It involves prioritizing maintenance work and organizing it so that it is completed efficiently.
Planning activities consider everything that will be needed for maintenance work to be performed, including: what tasks need to be done, how tasks will be performed, what parts will be needed, and who will do the work. Those involved in maintenance management must coordinate employee schedules and part availability with ever-changing maintenance priorities and asset availability.
Scheduling determines when jobs are performed. Some maintenance work is urgent and performed immediately, while other jobs are scheduled to be completed in the near future. Regularly occurring maintenance work, such as inspections and condition monitoring, is scheduled in advance at weekly, monthly, or even yearly intervals. Therefore, it makes sense that scheduled maintenance is planned in advance.
While it is not necessary for maintenance to be planned and scheduled, many organizations desire to move towards a proactive, rather than reactive, maintenance culture. In another section, we will describe the differences between proactive and reactive maintenance.
Maintenance Request Management
While much of an organization’s maintenance needs are handled within the maintenance department, other departments and employees may request maintenance assistance. Requests that come from outside the maintenance department must be reviewed and evaluated for their legitimacy. Valid, approved requests move on to become work orders.
In addition to receiving, reviewing, and accepting, maintenance request management includes communicating with requesters. Requesters expect to be informed about the status of their request, such as whether the requests have been approved, when work will take place, and whether the requested work has been completed.
Further Reading: What is a Maintenance Request System?
Reporting
As with all types of management, reporting plays an important role. Maintenance management reports inform the organization of different aspects of maintenance operations. Reports are used to collect key data about the maintenance department, track key performance indicators (KPIs), identify areas of improvement, and set goals. Reports also help the organization develop forecasts, guide budget planning, and make better decisions.
Maintenance Management Strategies
There is no one correct way to manage maintenance. Different types of maintenance management are used depending on factors such as the nature of the imminent or present failure, availability of parts and personnel, and budget.
Maintenance management generally employs one of two strategies: reactive maintenance and proactive maintenance. Both are acceptable maintenance processes and are often used in combination with one another. Yet, each involves a different amount of time and money. Organizations must be able to decide which methods to use and when.
Read: Keeping Assets Healthy: A Complete Guide to 4 Types of Maintenance
Reactive Maintenance Management
Some organizations choose a reactive maintenance management strategy, sometimes referred to in the industry as the firefighting method. With this strategy, maintenance teams wait until assets break before they take action to fix them.
As the term “firefighting” suggests, the circumstances surrounding this type of maintenance management are chaotic. Maintenance teams do not know when the next breakdown will happen, but spring into action once one occurs. Though this can place a burden on maintenance teams, especially when there are multiple “fires” to put out at once, it is a common way repairs are carried out.
The type of maintenance most associated with a reactive strategy is corrective maintenance (CM). Corrective maintenance tasks restore non- or under-performing assets to operational condition. They are typically performed in response to a critical failure or breakdown, though maintenance can be planned for less severe problems.
Proactive Maintenance Management
While some organizations take a “fix it when it breaks,” approach, others take a more proactive approach. They look to prevent failure by looking for signs of wear and tear before a problem occurs.
Proactive maintenance is performed in a number of ways. Assets are regularly inspected for signs of damage. Preventive measures, such as calibration, cleaning, and lubrication ensure assets function as expected. Pre-emptive part replacement reduces the chance of downtime caused by worn components.
Compared to reactive maintenance management, proactive maintenance requires more forethought and planning, but makes maintenance activities more predictable. The types of maintenance commonly associated with proactive maintenance are as follows:
- Preventive Maintenance (PM): Fixing small problems before failure can occur.
- Condition-based Maintenance (CbM): Using sensors to monitor an asset’s condition.
- Predictive Maintenance (PdM): Using sensors, historical data, and real-time data to predict when an asset will fail.
Maintenance Management: A Team Effort
As you have learned so far, maintenance management requires a lot of time, effort, and money to be effective. With so many resources to organize and manage, it would be hard to believe that a single person could manage maintenance alone – and you’d be right!
Maintenance management is a true team effort, involving many different people throughout the organization. Below are the most common roles that contribute to successful maintenance management.
Maintenance Managers
Maintenance managers, of course, lead the way when it comes to carrying out maintenance activities. They are primarily responsible for overseeing the installation, troubleshooting, repair, and maintenance of assets. This includes being in charge of the processes and resources that tie into performing maintenance, such as managing work orders, coordinating parts and labor, and planning and scheduling maintenance. At times, maintenance managers also perform maintenance work alongside their team.
Maintenance Technicians
Maintenance technicians carry out most of the maintenance work on a daily basis. They are the frontline, “boots on the ground” workers who complete the tasks assigned by the maintenance manager. Because they work closely with assets every day, technicians have a deep awareness of how to best care for them, what problems may arise, and how to respond.
In addition to performing maintenance, technicians are also responsible for documenting their work. This includes keeping a record of what was done, what parts were used, and how long the job took to complete. This data is used by others to improve maintenance planning, scheduling, and other decision-making.
Upper Management
Upper management and corporate executives are responsible for helping the organization hit their goals of increased profits and growth. As it relates to maintenance management, increased profitability can be achieved by lowering the costs maintenance incurs through labor and materials. Executives use the information they receive from the maintenance department to make strategic decisions related to standardization, budgets, and capital investments.
Other Departments
The maintenance team does not exist in a vacuum. Other departments, such as production, quality, and operations interact with – and rely on – the maintenance team to operate. These departments help to notify the maintenance team of ongoing or otherwise unnoticed maintenance needs. In return, the maintenance team provides them with functioning, reliable assets used for the production of goods or delivery of services. When things go wrong, these other departments rely on the maintenance team for help.
Maintenance Management Software
As you may have realized, maintenance management is complicated. Fortunately, there are tools like computerized maintenance management system (CMMS) software that simplify it.
A CMMS is a platform that gathers, stores, and organizes maintenance information in a central database. It is designed to manage maintenance activities and resources while keeping detailed maintenance records of all assets within an organization. With all of this data at their fingertips, industrial organizations can easily control their maintenance operations based on their maintenance strategy.
The CMMS supports all your needs related to managing work orders, assets, MRO inventory, planning and scheduling, maintenance requests, and reporting. Data stored in a CMMS is also used to help establish baselines and build asset maintenance histories. This information enables teams to analyze trends using key performance indicators (KPIs) and other reports, and identify areas of improvement.
Read our blog article, What is a CMMS? to learn more about maintenance management software.
FTMaintenance Maintenance Management Software
A computerized maintenance management system (CMMS) is the foundation of good maintenance management. A CMMS, such as FTMaintenance helps organizations maintain cost effective maintenance operations. In fact, companies that adopt a CMMS can improve their overall efficiency by up to 65%.
Whether you want to reduce machine downtime, save money on repairs, streamline your day-to-day workflow, or all of the above, a CMMS like FTMaintenance will help you reach these goals.
Learn more about how FTMaintenance helps manage maintenance activities by exploring our CMMS features and services.
Recent Comments