Key Takeaways
- Condition-based maintenance (CbM) is a proactive maintenance technique that focuses on real-time asset performance
- CbM alerts employees when equipment is performing outside of its specified range, prompting maintenance intervention
- Assets with high repair and replacement costs are good candidates for condition-based maintenance
- Computerized maintenance management system (CMMS) software, like FTMaintenance, tracks maintenance activities related to condition-based maintenance
What is Condition-based Maintenance?
Condition-based maintenance (CbM) is a proactive maintenance technique that uses real-time data (collected through sensors) to identify when an asset’s performance or condition reaches an unsatisfactory level. By observing the state of an asset, a practice known as condition monitoring, maintenance professionals can identify when an asset is about to fail or has failed. With CbM, maintenance work is performed only when needed in response to the asset’s real condition, preventing unnecessary maintenance tasks.
Condition-based Maintenance (CbM) vs. Predictive Maintenance (PdM)
Though condition-based maintenance and predictive maintenance (PdM) have some overlap and are often used interchangeably, they are not technically the same. CbM focuses on real-time asset performance and conditions, and alerts you the exact moment monitored parameters are out of bounds. For example, a sensor reading taken from an oil pump may show a major drop in pressure, indicating that a component has failed.
Predictive maintenance utilizes real-time asset data, like CbM, in addition to predictive analysis to determine when an asset will fail in the future. To continue our previous example, sensor readings from an oil pump may be used to forecast when an issue will occur or is beginning to form. As you can see, while both CbM and PdM use condition monitoring, the key difference is timing – what is the condition of an asset right now (CbM) versus what might the condition of the asset be in the future (PdM).
How Condition-based Maintenance Works
Condition-based maintenance consists of three steps: 1) capturing sensor data, 2) communicating data, and 3) performing maintenance work.
Capturing Sensor Data
Condition-based maintenance monitors asset performance through non-destructive testing carried out by condition-monitoring sensors. These sensors check conditions, such as vibration, temperature, and pressure, while assets are in operation. They may be provided by the original equipment manufacturer (OEM), be integral to the equipment, or purchased and retrofitted after initial installation. Common condition-monitoring sensors include:
- Accelerometers: Measure vibration, velocity, and displacement.
- Infrared Cameras: Detect heat and displays results on a thermal image.
- Fluid Condition Sensors: Observe the condition of a fluid such as oil.
- Tank Level Sensors: Monitor the level of fluid in a tank.
- Pressure Transducers: Measure the pressure of liquids and gases.
- Ammeters: Gauge the current running through a circuit.
Communicating Data
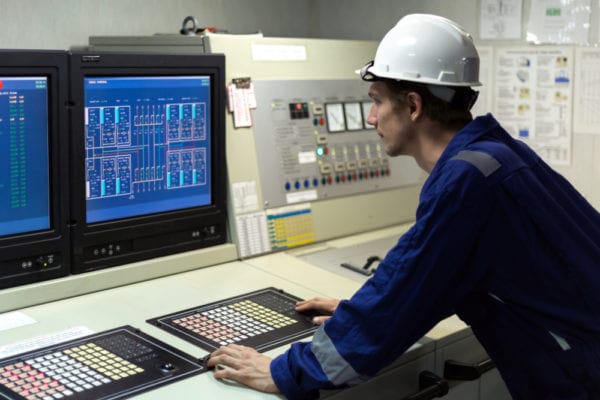
Trained maintenance technicians can view data captured by sensors to better understand an asset’s current condition before performing maintenance work.
Once a sensor has found that a monitored parameter is out of its normal operating range, it must communicate that information to a human employee who can provide a remedy. Notifications can take many forms. A programmable logic controller (PLC) that runs a machine may notify a technician that service is required in a variety of ways like, for example, turning on a stack light. A human-machine interface (HMI) or SCADA system may turn on a warning light, sound an alarm, display a message, or send a text or email notification. Computerized maintenance management system (CMMS) software may auto-generate a work order.
Performing Maintenance Work
When a monitored condition creates an alarm or notification, the maintenance team is dispatched to fix the problem. Based on the resolution, the maintenance team will create Standard Operating Procedures (SOPs) that provide technicians with step-by-step instructions on how to solve the issue. SOPs are then included on maintenance work orders generated by CMMS software, enabling technicians to respond faster and perform repairs with higher quality and consistency. Maintenance personnel also document their work in the CMMS once work is complete.
Advantages of Condition-based Maintenance
As part of an overall maintenance management strategy, condition-based maintenance provides the following advantages:
- Optimized Time Spent on Maintenance: Condition-based maintenance is performed as needed, maintenance teams can optimize the use of their time.
- Less Disruption of Production: Some issues identified by CbM can be corrected without shutting down equipment, ensuring higher availability for production.
- Lowered Chance of Catastrophic Failure: Condition-monitoring sensors catch problems the moment they happen, allowing technicians to respond quickly before more serious problems develop.
- Reduced Asset Downtime: When properly configured, CbM can be associated with specific failure modes. This allows the maintenance team to quickly diagnose possible causes, thereby increasing the speed of response times and reducing downtime.
Disadvantages of Condition-based Maintenance
Every maintenance approach has drawbacks. The following list outlines some of the challenges with CbM:
- High Sensor Costs: Cost of purchasing, installing, and maintaining condition-monitoring sensors and related software can exceed the total benefit of reduction on failures and downtime.
- Unpredictable Peak Times: Condition-based maintenance events are unplanned and may result in periods where multiple assets need attention at the same time.
- Difficulty in Choosing Sensors: Sensors come in many different types, sizes, and shapes, making it a challenge to select the right one.
- Reliability of Sensors: Sensors installed and used in harsh locations have the potential to become damaged, perform incorrectly, and provide faulty readings. Wireless sensors rely on the strength of the company’s Wi-Fi signal to consistently communicate data.
- Required Expertise: A high level of technical knowledge by staff is necessary to implement and maintain sensors, use related software, and interpret sensor data.
When to Use Condition-based Maintenance
The decision whether to use condition-based maintenance depends on the expected return on investment (ROI). Organizations must assess the amount of risk involved if an asset fails by asking questions like:
- How critical are potential failures?
- What does it cost to resolve failures?
- Are those failures likely to recur?
Highly critical production assets with high repair and replacement costs are usually the best candidates for a condition-based maintenance program. Typically, CbM is used in large, asset-intensive organizations including automotive suppliers, oil and gas, facilities with complex building automation systems, utilities, and organizations that rely on fleet vehicles.
Read On: Explore our Industries page to see how FTMaintenance supports your industry.
FTMaintenance Supports Condition-based Maintenance
Maintenance professionals track condition-based maintenance activities in CMMS software like FTMaintenance. FTMaintenance provides a single platform for documenting, managing, and tracking CbM work orders and maintenance resources. Schedule a demo today to discover how FTMaintenance can support your condition-based maintenance operation.
Recent Comments