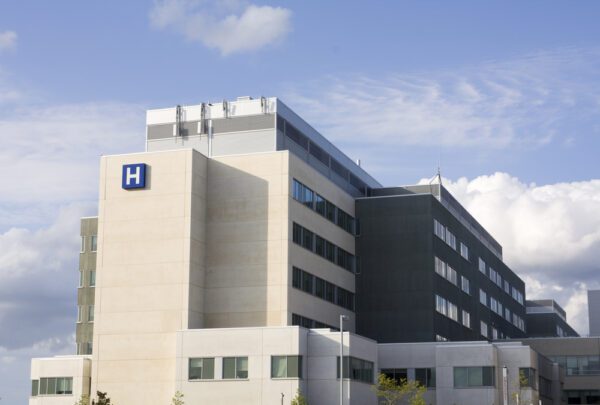
Key Takeaways
- Hospitals and healthcare facilities face numerous maintenance challenges not experienced in other industries
- Healthcare facility maintenance is crucial for ensuring safety, security, and functionality, particularly as it applies to the patient experience
- Hospitals can leverage a CMMS to optimize healthcare facility maintenance and operations
Healthcare facilities are a complex ecosystem of interconnected systems and spaces designed for patient care, administrative and support functions, and facility operations. These characteristics set hospitals and similar facilities apart from other types of buildings, posing unique maintenance challenges for healthcare facility managers. To overcome these obstacles, facility managers rely on computerized maintenance management system (CMMS) software to gain better control over maintenance operations.
What is Healthcare Facilities Management (HFM)?
According to the Occupational Safety and Health Administration (OSHA), hospital facility management is “an interdisciplinary business function that coordinates space, infrastructure, people, and organization in the hospital. It is responsible for the management and coordination of work projects for the construction, renovation and ongoing maintenance of the infrastructure at the hospital.”
As we covered in our article, What is Facility Management?, facility management involves hard and soft services. To recap, hard facility management services relate to the physical building, and include functions such as preventive maintenance, capital improvements, and management of building systems. Soft services focus on the people who use the building, encompassing responsibilities such as security, emergency preparedness, and janitorial services.
Role of the Maintenance Department in Hospitals and Healthcare Settings
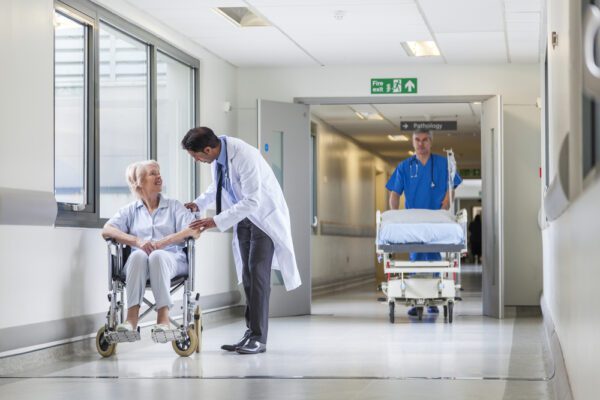
Numerous stakeholders are affected by the healthcare facility’s condition and performance, causing maintenance activities to be heavily scrutinized.
People go to healthcare facilities to check, keep up, and restore their health. They expect buildings to be safe, secure, and functional. Maintenance teams work tirelessly behind the scenes to ensure medical buildings run at their best, so as to not introduce any risk that may compromise the quality of healthcare services. But it’s not just patients who feel the effects – the condition of healthcare facilities affects everyone who enters the building including doctors, nurses, support staff, and visitors.
Apart from the people who work in and use hospitals, those who own and manage healthcare facilities also have a vested interest in maintenance as well. First off, maintaining a hospital is costly. It is estimated that operations and maintenance accounts for 80-85% of a healthcare facility’s capital project dollars, with maintenance occupying most of a facility manager’s responsibilities. Aside from costs, ownership must carefully monitor how the effectiveness of healthcare facility maintenance affects patient satisfaction, reputation, insurance reimbursement, and legal liability.
Challenges of Hospital Facility Maintenance
Every industry faces its own set of unique challenges, and hospitals and healthcare facilities are no different. Below are some examples of what makes healthcare facility maintenance so complex.
Round-the-clock Maintenance Operations
Hospitals bustle with activity both day and night. Maintenance teams are responsible for keeping critical building systems in operation at all times. This presents a major challenge for hospital maintenance – finding time to perform scheduled maintenance without causing downtime.
Round-the-clock operations require skillful planning and scheduling. First, if primary equipment must be taken offline for maintenance, a backup or alternative must be arranged. With limited backups available, assets must be maintained on a staggered schedule, creating a constant flow of maintenance work.
Further, maintenance must take any chance they can get to perform routine maintenance tasks. Maintenance schedules should be flexible enough to accommodate changing priorities, off-hours, or emergencies.
Adding to the administrative demands of planning and scheduling is the communication of maintenance tasks and coordination of resources. 24/7 operations means that responsibilities are handed off between shifts, and maintenance activities must be effectively communicated to new staff arriving to work.
Equipment Reliability
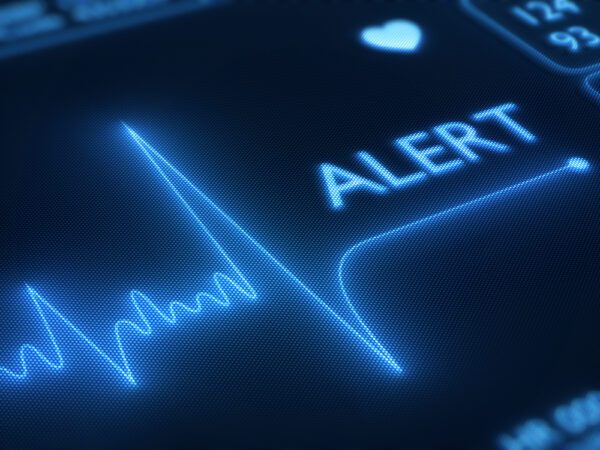
Managing the maintenance needs of diverse hospital assets is complicated, resource-intensive, and requires careful attention. Building systems, medical equipment, and infrastructure are in constant use, so they wear out faster and require more frequent maintenance. However, each asset has its own unique maintenance needs, which adds to the complexity of asset maintenance.
More concerning is that any failure can set off a chain reaction with serious consequences. Treatment may be delayed or rescheduled, causing dissatisfaction with patients. Medical procedures may become complicated or carry heightened risk of infection (or worse). Hospitals may also violate compliancy requirements and suffer legal ramifications.
Further, a large number of healthcare assets naturally lead to a high volume of service requests and work orders. Unlike in standard facilities, where work orders may be prioritized by cost and complexity, maintenance work in hospitals must also consider the potential effects on patient care.
Regulatory Compliance and Safety
A 2017 American Hospital Association (AHA) study revealed that healthcare facilities must comply with as many as 629 requirements from the following 4 agencies:
Hospitals must also follow other regulations set by the OSHA and state health departments. In addition, healthcare facilities also seek accreditation from organizations such as:
Needless to say, there are an overwhelming number of regulations healthcare facilities must adhere to that are not required in other types of facilities. These regulations are constantly changing to keep up with evolving healthcare concerns.
Healthcare regulatory requirements are stringent, especially when it comes to patient safety, infection control, safety systems, and environmental issues. Facility managers must invest in the proper equipment, training, and documentation systems in order to meet compliancy requirements. This can be difficult with limited budgets and resources. In fact, the AHA estimates that healthcare facilities spend approximately $39 billion each year in order to comply with the administrative aspects of regulatory compliance.
If hospitals are found to be out of compliance, they can be penalized with fines, loss of accreditation, and exposed to legal liability. Therefore, it is critical that everyone involved with hospital facility maintenance and management understands their regulatory obligations and the risks that non-compliance poses to patients, staff, and the hospital at large.
While specific regulations differ globally, healthcare facilities across the world face similar challenges in maintaining safe, compliant environments. For example, Mitie, the UK’s leading healthcare facilities management company, supports healthcare organizations in upholding high service standards and meeting compliance requirements with tailored support services.
Resource Constraints
As in most industries, budget limitations and staffing shortage pose significant challenges to healthcare facility maintenance. When budgets are constrained, maintenance teams must find ways to lower costs without compromising patient care. This typically comes in the form of optimizing inventory management, prioritizing critical assets for preventive maintenance, reducing energy usage, and adopting lean maintenance techniques such as total productive maintenance (TPM).
In addition to budget constraints, hospital maintenance teams must also contend with staffing shortages. In hospitals, stress and burnout extend to all employees and make potential hires reconsider working in the healthcare field. This is especially true following the COVID-19 pandemic.
Another issue is that the maintenance workforce is getting older and there simply aren’t enough new, qualified people to replace them. Given the compliancy demands, hospitals prefer technicians to have healthcare experience, further limiting the pool of candidates. These labor market forces require hospitals to find ways to attract new hires and retain veteran staff.
Cleanliness and Hygiene
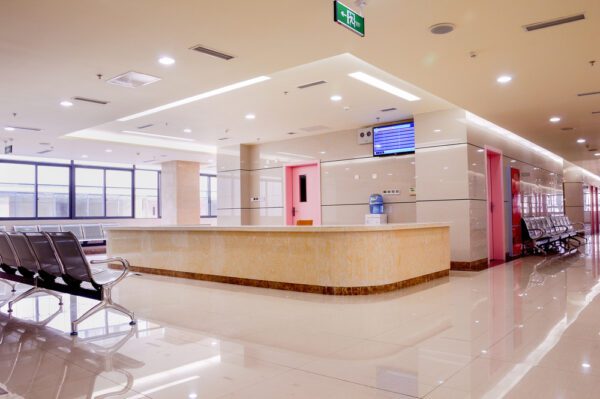
Maintaining clean and infection-free environments presents numerous challenges. On top of regular maintenance duties and compliance requirements, facility management teams must also maintain rigorous cleaning and sanitation standards. Beyond routine cleaning, teams are also responsible for proper waste disposal, infection control, and air quality management. Even factors as seemingly small as making sure there is enough sunlight and ventilation play a role in creating a hygienic, germ-free facility.
These efforts are crucial for reducing the spread of germs and preventing healthcare-associated infections (HAIs), which can lead to severe illness, even death.
Benefits of CMMS for Healthcare Facilities
If not addressed, the challenges we discussed earlier can lead to dire consequences. A computerized maintenance management system (CMMS) offers numerous benefits to healthcare facilities, providing the tools needed to tackle these challenges head on. Below are just some of the many benefits hospitals gain from using a CMMS.
Centralize Asset and Inventory Data
A CMMS brings all of your asset and inventory information together in one place, providing you and your team with a single source of truth about your maintenance assets. The system helps you build an asset registry to track equipment individually, ensuring that each piece of equipment receives a maintenance schedule and is accurately documented. CMMS software that supports asset tagging through barcoding allows you to track your assets, their location, and related work orders.
Tracking your inventory in the CMMS helps you quickly locate information about spare parts and tools, such as where they are located, how many are in stock, or who possesses them. Automatic stock updates reduce the likelihood of maintenance tasks being delayed by stockouts and wasting money on unnecessary purchases.
Further Reading: 3 Asset Naming Convention Designs to Consider
Maximize Asset Uptime
Using healthcare maintenance software enables you to implement proactive maintenance strategies. By creating a master preventive maintenance schedule for each asset, you can address potential issues before problems arise. This ensures that critical equipment and infrastructure remains operational without disrupting patient care.
Automatic work order activation and notifications ensure that necessary preventive maintenance work doesn’t fall through the cracks, and that technicians are aware of upcoming repairs. With a proactive mindset and robust maintenance schedule, you can significantly reduce downtime and extend asset life.
Easily Provide Documentation for Audits
Tracking maintenance activities in a CMMS makes it easy to provide the documentation required for maintenance audits. A user-friendly interface makes it easy for technicians to demonstrate how they perform regular tasks such as generating and closing work orders and updating asset records. Using task lists, you can create standard maintenance procedures (SMPs) that include step-by-step instructions and ensure compliance with internal policies and regulatory standards. Some systems even include change log functionality that tracks what changes were made, who made them, and when.
Access Your CMMS On-the-Go
A mobile CMMS bring the power of your CMMS into the hand of technicians wherever they go. Using a streamlined interface, maintenance teams can stay productive no matter where they are throughout the facility, and reduce time otherwise wasted returning to a central office. Barcode scanning capability helps maintenance technicians quickly access asset details, while cameras can be used to provide supplemental visual aids to work orders. Offline modes allow the CMMS to be used in areas with poor or no internet connectivity.
Keep Your Facilities Healthy with FTMaintenance Select
The complexity of healthcare facilities presents numerous challenges not found in other industries, especially as it relates to the patient experience. With so much on the line, it is critical that maintenance teams are equipped to handle the demands of hospital maintenance.
FTMaintenance Select is a comprehensive CMMS solution that provides your team with tools necessary to support the well-being of patients and staff. It centralizes your maintenance data in order to help you improve operational efficiency, implement proactive maintenance strategies, effectively coordinate resources, and simplify documentation practices. Request your demo today to see how FTMaintenance Select keeps your facilities running smoothly.
Read more about FTMaintenance Select benefits for healthcare facilities
Recent Comments