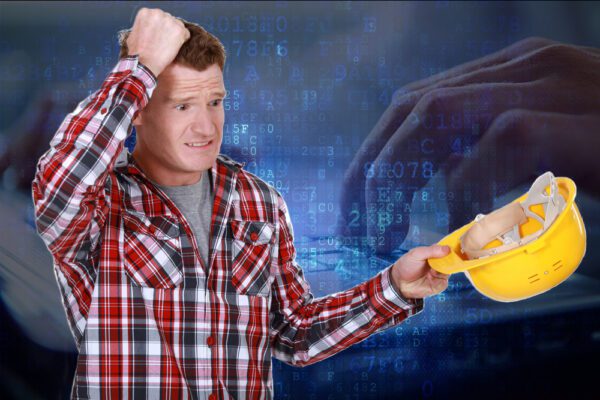
Industrial organizations continue to invest in computerized maintenance management system (CMMS) software in pursuit of greater efficiency to increase asset reliability and reduce maintenance costs. However, the urgency of CMMS implementation often leads to organizations overlooking the importance of maintenance data quality.
As a result, bad data is entered into the CMMS from the start, disrupting maintenance operations and setting your team up for failure. In this article, we’ll examine the consequences of poor quality CMMS data and what you can do to ensure your CMMS delivers value to your organization.
What is Data Quality?
Data quality generally refers to the extent to which information is fit for its intended purpose and correctly reflects the real-world entities it represents. In a maintenance management context, this means ensuring that maintenance records accurately document and reflect the true state of assets, inventory levels, and resource availability.
The quality of your maintenance data is critical for making decisions related to asset lifecycle management, maintenance scheduling, resource allocation, and other maintenance management processes. Therefore, you must ensure that you are working with high quality data. Poor-quality data makes these decisions more difficult and leads to real-world consequences. For example, a Gartner report estimates that organizations lose an average of $12.9 million (USD) each year due to poor quality data.
What Makes Data High-Quality?
Recognizing poor-quality data is easier said than done. Within a dataset containing hundreds to hundreds of thousands of CMMS records, it can be difficult to distinguish the “bad” data from the “good” data. So, what is meant by “high-quality” data after all?
Data quality is measured by comparing your data to a desirable state. High-quality data is commonly defined by the following characteristics:
- Accuracy: The data correctly represents what it is intended to represent.
- Completeness: All necessary data is available.
- Consistency: The data exactly matches across all places where the data is stored and used.
- Currency: The data was recently collected and/or reflects the most up-to-date information.
- Relevancy: The data serves a meaningful purpose.
- Timeliness: The data is available within the expected timeframe.
- Uniqueness: The datum is not duplicated within the set of data and is uniquely identified.
- Validity: The data is properly structured according to defined rules and parameters.
Maintenance data that meets these criteria provides a strong foundation for informed decision-making, ensuring maintenance teams can rely on facts rather than gut feel. This data-driven approach helps you make better recommendations and strengthens your credibility within the organization.
Types of CMMS Data
CMMS solutions allow you to manage several types of data, each playing a role in effective maintenance management. Understanding the types of data in your CMMS and what the data represents is essential for evaluating data quality. This knowledge helps you become familiar with what maintenance records should look like, and makes it easier to identify poor-quality data. The primary types of CMMS data include:
Asset Data
Asset data refers to information about your physical assets and equipment. This includes:
- Asset identification numbers: Unique identifiers that are used to track assets.
- Current condition: The asset’s operational status and overall health.
- Location: Where the asset is physically located within the organization.
- Operating specifications: Operating parameters, such as capacity, power requirements, safety standards, and other performance requirements.
- Downtime, meter readings, and other performance data: Relevant metrics related to the asset’s availability and reliability.
Work Order Data
Work order data captures the performance of maintenance activities, including what was done, who did it, and what resources were used, among other information. Work order data typically includes:
- Details: Essential data about the work order such as its unique number, completion status, priority, assignment, and relevant life cycle dates.
- Tasks: The specific actions taken to perform the work outlined by the work order.
- Parts and tools: The materials and supplies, and quantities of such, required to carry out the maintenance tasks.
- Labor resources: The people or organizations that performed the work and their labor hours.
MRO Inventory Data
MRO inventory data is the information related to your inventoried assets and consumables. Inventory data can include:
- Inventory identification numbers: Unique identifiers used to track MRO items.
- Stocking location: The exact location within a stockroom or other inventory location where parts are stored.
- Quantities: The level of stock on hand, allocated to work orders, and available to use.
- Procurement information: Information related to replenishing stock, such as reorder point, economic order quantity, and supplier information.
Labor Resource Data
Labor resources are parties that provide labor for an organization, whether it is an employee, vendor, contractor, or other service provider. Examples of labor data include:
- Labor resource information: The names of the labor resources.
- Role and skills: The job title, department, labor craft, type of services provided, and other applicable skill information.
- Certifications: Documentation of any formal training or certifications held by the labor resource.
- Labor costs: The hourly rate for work performed by a labor resource.
Maintenance History
Maintenance history is a record of all past maintenance activities. CMMS solutions automatically create a maintenance history using closed work order records.
Other Management Data
Management data provides essential insights that help maintenance managers and other decision-makers assess performance, control costs, and optimize operations. This data includes:
- Key performance indicators (KPIs): Measures of performance. Common KPIs include Mean Time to Repair (MTTR), Mean Time Between Failures (MTBF), and maintenance backlog.
- Cost information: Information related to the overall expenses incurred by the maintenance team. For example, costs related to labor, parts and materials, and operations.
- Scheduling data: Information that outlines planned maintenance activities including task frequency, labor availability, and stock replenishment.
The Ripple Effect: How Poor-Quality CMMS Data Impacts Maintenance Operations
On the surface, a little compromised data in your CMMS may seem like a minor issue. After all, could a little bad data really be that bad? To put it simply, yes. Even small errors and inconsistencies can have big implications and lead to costly consequences. Let’s look at a few examples of this ripple effect in the real world.
Example 1: Asset Record Duplication
Suppose an asset is entered into the CMMS multiple times under different record IDs. When users encounter the duplicated records, they choose one using their best judgment or out of convenience, which results in maintenance activities for the same asset being tracked across multiple records.
This split results in incomplete asset data, redundant maintenance events being scheduled for the same asset which wastes time and resources, and difficulty in generating maintenance reports that track asset management KPIs.
Example 2: Inaccurate Inventory Data
It is safe to assume that nearly every maintenance department has dealt with the consequences of inaccurate inventory data. Outdated or inaccurate stock levels can lead to too much or too little inventory, both of which present challenges for maintenance teams.
When the CMMS incorrectly shows low stock for a part, it can trigger unnecessary purchasing activity. Even though the part is actually available, reordering it results in overstock, which ties up money and takes up physical space in the stockroom. Worse yet, these excess parts may become obsolete before they are used.
On the other hand, stockouts can occur when the CMMS indicates that a part is available when, in reality, it is not. This mismatch can lead technicians to proceed with maintenance work under the impression that parts are available, only to discover they are not actually in stock. As a result, costs are incurred due to excess downtime and emergency orders with premium shipping fees. Stockouts are especially problematic for highly specialized parts, which may have long lead times for replenishment.
Example 3: Failure to Meet Compliance Requirements due to Incomplete Records
Organizations in highly regulated industries like food and beverage and pharmaceuticals face rigorous maintenance audits to ensure compliance with safety protocols and regulatory standards. When a CMMS contains poor-quality maintenance data, the consequences can be severe.
For example, if task information related to critical equipment maintenance is incomplete or missing, auditors cannot verify that necessary inspections or repairs took place. This lack of verification can lead to costly fines, product recalls, or even shutdowns by regulatory bodies.
Additionally, poor-quality data makes it challenging to address violations promptly, as valuable maintenance resources must be dedicated to tracking down the correct information. This delay can expose organizations to additional penalties and heightened scrutiny in the future. Continued non-compliance can increase liability, damage the organization’s credibility, and undermine its ability to do business.
As you can see, the effects of poor-quality data are far-reaching, disrupt maintenance operations, and negatively impact maintenance efficiency.
Common Causes of Poor-Quality CMMS Data
Bad data comes from various sources, but a handful of factors are responsible for most CMMS data quality issues. Understanding these sources is essential for preventing poor-quality data in the first place. Here are the top causes of poor-quality data:
Human Error
People make mistakes. When data is entered by hand, there is a risk of typos, skipped fields, and other data entry errors. One study found that as much as 4% of manually entered data contains errors. Other studies have found that up to 5% of data contains errors, depending on its complexity.
While this number may seem small, consider that CMMS systems contain hundreds or thousands of records, meaning that dozens of critical maintenance records may contain inaccuracies. Not only can this poor quality data lead to misinformed decisions, it also raises doubts about the reliability of other data in the system.
Lack of Standardization
Standardization refers to entering data consistently based on pre-defined rules and formats. Without standardization, CMMS data may be entered in various formats, spelling, or abbreviations, which leads to further errors and confusion. For example, one user may enter an asset number as “Pump 1,” while another user enters “Pump 001” or “P-1”. These inconsistencies make it harder to track the asset because multiple naming conventions prevent accurate search results and may cause the asset to be left out of valuable maintenance reports.
Read More: What is an Asset Naming Convention?
Duplication
Whether created out of convenience or in error, duplicate records cause big problems in a CMMS. Duplication splits maintenance history across multiple records, making it difficult to track performance and costs, identify failure patterns, or schedule preventive maintenance. Because one user might be unaware of the duplicated record, maintenance activities may be scheduled more frequently than is necessary, resulting in over-maintenance and wasting precious resources.
In the context of MRO inventory management, duplicate records can cause serious overstock, as multiple records may trigger unnecessary orders for the same part. Not only does this cost money, the excess parts take up valuable space in the stockroom.
CMMS Software-related Issues
Sometimes, a CMMS solution’s design or lacking configuration options can lead to poor-quality data. For example, when essential fields for capturing maintenance data are missing, users will enter information into any other available fields, even if they weren’t intended for that purpose. Systems that lack sufficient field validation allow users to enter data in non-standard formats, creating inconsistencies.
Additionally, systems that don’t include configuration options such as mandatory fields and dropdown field customization leave the system susceptible for errors. The reliance on manual data entry without automation also significantly increases the risk of human error.
How to Fix – or Prevent – CMMS Data Quality Issues
Poor-quality CMMS data can be a widespread problem, but the good news is that there are effective ways to fix or prevent these data quality issues. Ideally, bad data is caught before being entered into the CMMS. However, if poor-quality data does make its way into the system, either through direct import of legacy data or through manual entry, there are ways to address it. Below are some strategies to consider.
Clean Your Data
As the saying goes, “garbage in, garbage out.” When it comes to data quality, this means that entering poor-quality data into your CMMS will lead to poor-quality results. Therefore, organizations should prioritize data cleaning. Data cleaning is the process of identifying and fixing errors within a dataset so that it is accurate and usable. Common steps include resolving duplicate records, updating outdated information, and removing irrelevant data. For best practices on preparing maintenance data for import, check out our article Best Practices for Preparing Maintenance Data for CMMS Import.
Data cleaning is particularly important for organizations transferring data from a legacy CMMS, spreadsheet, or other in-house solution into a modern CMMS. Too often, organizations focus solely on migrating data into the new system without analyzing their existing data. As a result, maintenance teams struggle to derive value from the new system because they continue to work with flawed data.
Establish Data Entry Standards
Creating and enforcing data entry standards is vital for ensuring consistent data across the CMMS. This includes designing an asset naming convention, setting required fields, and defining appropriate formats for data, such as dates or numerical values. To help users adhere to these standards, the CMMS can be configured with required fields and field validation rules. Additionally, offering users pre-selected values instead of allowing free-form entry can further minimize errors.
Regularly Audit Maintenance Data
Resolving data quality issues is an ongoing process. Humans are prone to make mistakes from time to time, and the software can’t realistically prevent every error. Therefore, it is important that administrators regularly audit CMMS data to ensure that standards are being followed.
Schedule periodic reviews to ensure that all assets are tracked in the system, all required data is being entered, and that users are following a consistent format. Depending on the size of your dataset, consider spot checks that randomly assess a subset of records for accuracy.
Provide Regular Training
Proper training ensures that technicians can effectively utilize the CMMS and maintain high data quality. Since technicians are primarily responsible for data entry, it is critical that they are well-equipped with the knowledge and skills needed to enter good data.
Training sessions should emphasize the value of accurate data by helping them understand how their data entry responsibilities impact maintenance operations. In addition, technicians should receive thorough instructions on how to navigate the CMMS and input data correctly. Vendor-provided training, user manuals, and step-by-step guides for common tasks are valuable resources for reinforcing best practices and minimizing errors.
Learn more about FTMaintenance Select training
Maximize the Value of Your Maintenance Data with FTMaintenance Select
High-quality CMMS data is the backbone of effective maintenance management. Accurate, consistent information empowers you to make strategic maintenance management decisions that minimize downtime, improve performance, and control costs. Though maintaining data quality is challenging, the costly and widespread consequences of poor data are worth avoiding.
Implementing a CMMS, like FTMaintenance Select, presents the perfect opportunity to establish strong data quality management practices. FTMaintenance Select provides a centralized platform that helps you organize your maintenance data, making it easier to track, manage, and maintain data quality. By bringing together all of your critical asset, work order, inventory, and resource information in one place, you can ensure consistency across your data and reduce errors. With accurate, reliable data at your fingertips, you can make informed decisions that optimize maintenance operations.
Request a demo today to learn how FTMaintenance Select can provide the insights you need for successful maintenance management.
Recent Comments